Ensuring workplace safety is paramount for high-risk sectors committed to workplace resilience and the well-being of their employees.
One of the critical safety metrics of occupational safety is the Lost Time Incident Rate (LTIR). It serves as a key indicator, providing insights into the frequency and severity of work-related incidents that result in lost workdays.
In this article, we’ll see how you can approach calculating LTIR, and foster a culture that prioritizes the health and safety of your people.
Contents:
What Is the Lost Time Incident Rate?
The Lost Time Incident Rate is an Occupational Safety and Health Administration (OSHA) metric that calculates the number of incidents that result in time away from work.
Despite the designation of lost time in the calculation, OSHA does not use such terminology when referring to absenteeism because of injury or illness.
It refers to lost time as a lost workday case. For OSHA recordkeeping purposes, they advise that lost workday cases account for days away from work or days of restricted work activity beyond the date of the injury or onset of the illness. OSHA standards also advise that records exclude holidays, vacations, or other days an otherwise healthy employee would not work.
The LTIR does not assess the gravity or severity of injuries nor the time lost because of each injury. The primary purpose of the metric is to calculate the number of lost time incidents per so many employees.
LTIR Formula
The lost time incident rate formula: (lost time injuries / total hours worked) x 200,000 = LTIR per 100 employees
Calculating LTIR is straightforward. Take the number of lost time injuries, divide by total hours worked, and multiply by 200,000. This final figure shows how many incidents per 100 employees led to lost work time, highlighting trends that might be impacting productivity on-site.
For example, if a company experiences two lost time injuries over a period in which employees worked a combined total of 175,000 hours, the LTIR would be calculated as follows:
- Divide 2 (lost time injuries) by 175,000 (total hours worked).
- Multiply the result by 200,000.
This calculation would give an LTIR of 2.29, signifying 2.29 lost time incidents per 100 employees.
What Is a Good LTIR?
A good Lost Time Injury Rate is a liquid concept. It can vary widely based on the industry, as each sector has unique hazards and operational conditions.
For example, industries like construction and manufacturing tend to have higher LTIRs due to the physical nature of the work, while finance or IT generally have lower rates due to the office-based environment.
To get an idea of what constitutes a “good” LTIR for your industry, see the benchmarks from the U.S. Bureau of Labor Statistics (BLS). They provide a standardized measure, using which you can compare tour safety performance against national averages within specific categories.
Why Is LTIR Important?
This metric is a vital measurement of your organization’s safety performance. A higher number shows a disregard for employee safety, which can affect insurance premiums and turnover rates. Also, too many incidents result in significant lost time, poor company performance and publicity.
The LTIR provides insight into past performances and helps leaders focus on problem areas and prevent similar incidents. To make this process more efficient, you can use automation tools that reduce the risk of human error in data entry and calculations.
What’s more, specific tools can centralize the LTIR data, providing a single source of truth, reducing redundancy, and facilitates better collaboration among your safety teams.
The Ultimate Guide
to Safety Inspections
Essential tools, customizable templates, and expert tactics to help you improve your inspection process
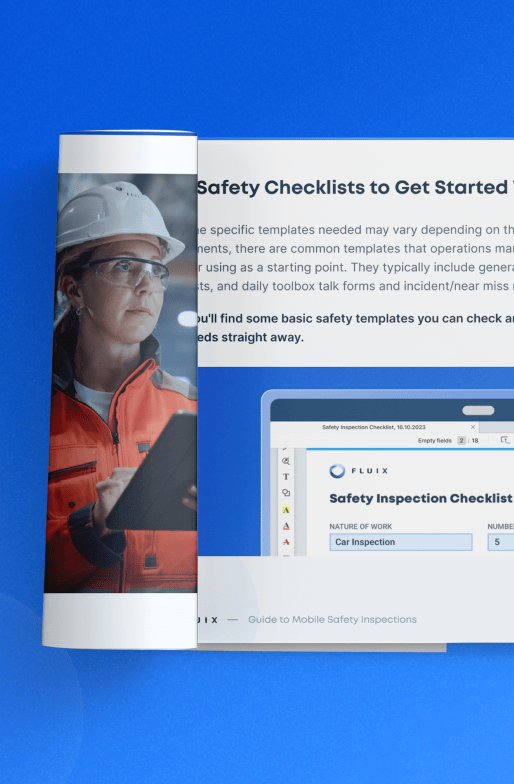
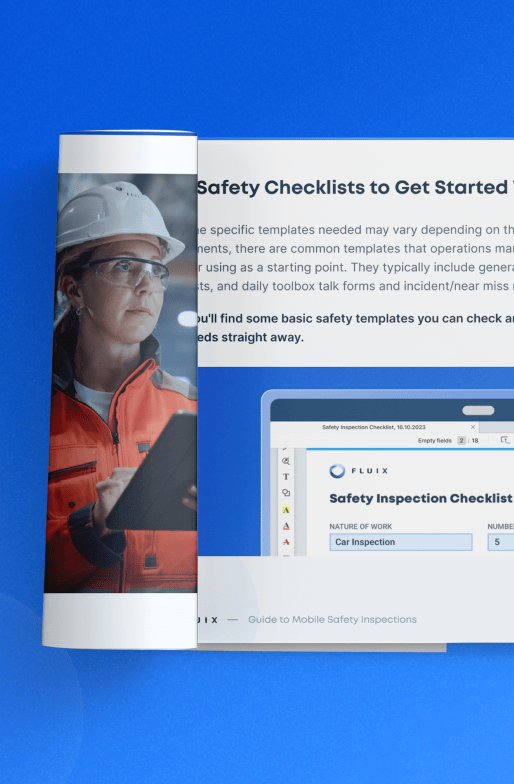
5 Steps to Reduce LTIR
Lowering or reducing your company’s LTIR means taking a systematic approach to upgrading your safety program. And the only genuine way to lower the metric is by reducing employee injuries.
While creating and distributing essential safety documents is core to all safety programs, taking care of safety policies and education is also helpful.
Here are five decisive actions you can take to improve a lost time incident rate within your organization.
1. Prioritize Safety Culture
Install a safety culture by making it a core value woven into every aspect, from leadership messages to daily operations.
Easier said than done, but here are some practical steps:
- Investing in safety training: Equip your team with the knowledge needed to respond effectively to emergencies. For example, schedule quarterly hands-on sessions that simulate common hazards people may encounter on-site.
- Encouraging communication: Create an environment that values open safety communication. For example, hold regular safety huddles or toolbox talks.
- Recognizing and rewarding safe behaviors: For example, create a points-based recognition program where people earn points for consistent safe behaviors.
2. Fight the Monotony of Hazard Assessments
Effective risk management is a crucial step in reducing LTIR. Identifying potential hazards in the workplace and implementing appropriate control can significantly contribute to preventing accidents and injuries that lead to lost time.
However, given the inherent monotony of this process (due to its repetitive nature), safety officers often become accustomed to the routine, and may overlook potential hazards. This results in under-reporting and ineffective control measures, at the same time decreasing engagement of your field staff in safety processes.
There are ways to avoid this:
- Introduce diverse methods for hazard assessments, using a combination of walkthrough inspections, employee surveys, and tools to keep the process dynamic.
- Rotate the responsibilities of people involved in hazard assessments.
- Provide ongoing training to employees, keeping them informed about new safety protocols, tools, and technologies.
- Incorporate safety management software, like Fluix, to digitize and streamline the hazard assessment process.
3. Apply a Black Box Approach to Incident Investigation
Experienced safety officers know that reducing the lost time incident rate requires more than just creating and filling out an incident report form. When incidents occur, documenting them is an initial step, but the real value lies in understanding why they happened.
Think of the principles of black box thinking they use in the aviation sector. Just as aviation investigates every mishap to uncover its root cause and prevent similar occurrences, your safety management should adopt a similar approach. And to make this work, you need the corresponding tools. Software for incident reporting with real-time data capture, root cause analysis capabilities, and automated reporting workflows may be a good starting point.
Tools like Fluix, Donesafe or SafetyCulture are created to automate the distribution and creation of incident reports, ensuring that relevant team members are promptly informed. More importantly, they facilitate collaboration by providing a centralized platform for incident documentation.
4. Promote Effective Communication
Straightforward as it may seem, discussing safety can actually improve safety. By regularly delivering toolbox talks, meetings or memos you encourage an open dialogue with employees about safety concerns.
Also, you can encourage participation in safety measures by recognizing and involving employee safety champions or empowering safety teams that can motivate and guide peers. Champions, teams and leaders can recognize and reward individuals and teams for achieving safety goals and milestones or who show commitment to safety practices.
5. Use an Advantage of Data Analysis
Finally, you can use data to improve a company’s LTIR. Every organization should review its LTIR routinely to identify trends and areas for improvement. The regular tracking of the metric allows you to set a benchmark, which helps frame future safety discussions, adjustments and practices.
By employing statistical analysis, preventive measures can be implemented to address the identified risks and reduce the likelihood of future incidents. Continuous improvement, based on a data-driven approach to safety, fosters a safety culture, with training and communication targeted at specific areas highlighted by the data.
How Fluix Can Help You Manage LTIR Documentation
Fluix is a field productivity tool that can help you simplify the entire documentation process, from incident reporting to compliance tracking and corrective actions. Here’s how:
- Automated Incident Reporting. Your teams can report incidents from the field, capturing critical information in real-time.
- Centralized Document Management. All incident reports, safety inspections, and corrective actions are stored securely in one centralized location.
- Automated Follow-Up Actions. Assign and track corrective actions, minimizing recurrence.
- Real-Time Analytics. With analytics dashboard, you can monitor tasks and statuses of LTIR related documents in real time.
- Audit-Ready Records. Fluix organizes all LTIR-related documents in a compliant, easily searchable format, making it simple to generate reports for internal audits or regulatory reviews.
By using these features you can standardize and consistently implement safety protocols across your job sites, teams and locations.