Behavior-based safety, commonly called BBS, aims to identify and reinforce safe behaviors while reducing unsafe practices in the workplace.
This approach focuses on the human side of safety, recognizing that employee behavior plays a pivotal role in accident and injury prevention.
Let’s explore the concept of BBS safety, and review practical steps for its workplace implementation, including using professional EHS software.
Contents:
What Is Behavior-Based Safety?
Behavior-based safety is a proactive approach to safety management that involves observing and modifying worker behavior.
Engaging in BBS safety requires a systematic process to identify, measure and ultimately change unsafe behaviors into safe practices.
While traditional safety programs focus on compliance with regulations and procedures, BBS engages employees in education and prevention at all levels.
Pros and Cons of Behavior-Based Safety
On the positive side, BBS fosters a proactive culture where employees actively participate in hazard prevention practices, leading to a more safety-conscious workplace. In addition, BBS safety programs can:
- Reduce the number of workplace incidents by taking effective steps to detect and change unsafe behavior. For example, one of such steps can be implementing automated systems for managing your safety files and reports.
Read more: Read more: Paper vs. digital: why it’s more secure to manage your safety documentation with software
- Empower employees by involving them in all stages of the process from identifying hazards to suggesting improvements, thus enhancing team commitment and accountability.
- Improve the efficacy of your company’s safety interventions by supporting data-driven decisions.
On the other hand, managers should consider certain factors before jumping into a BBS initiative. Without leadership communication and support, this approach can result in a few employees being singled out for unsafe behaviors.
The resulting blame culture harms worker morale and trust. Some critics of BBS cite an overemphasis on worker behavior without uncovering systemic issues.
To succeed with this approach, it’s important to devote the necessary time and resources to BBS so that teams can train observers, conduct the observation process, and plan and implement interventions in response to their findings.
Without an ongoing effort, the organization can become complacent and miss new safety concerns that emerge.
Real-World Behavior-Based Safety Examples
Reviewing BBS safety examples can inspire you as you incorporate this strategy at your own site.
In one case study reported by the Center for Behavioral Safety, an engine parts manufacturing facility with 476 employees engaged in a BBS initiative. Volunteer salaried and hourly workers received observer training in two eight-hour sessions, then spent nine weeks making behavioral observations during both the first and second shifts.
The observers used behavioral checklists to note unsafe practices. Facilitators collected these checklists twice a month and held team meetings to review the findings.
They also posted safety metrics on a public bulletin board. An evaluation 18 months after the facility started the BBS initiative found that days lost to illness or injury dropped from 10.9 to 1.5 per month on average.
And speaking of checklists usage, we also have an example to share.
One of our aviation customers, Panorama Helicopters, improved their safety management with the help of Fluix’s electronic flight bags, checklists, and automated communications.
More, the American Psychological Association reported several successful examples of BBS safety. For instance, Pool California Energy Services decreased finger, wrist and hand injuries by more than half within 12 months after adopting a BBS program. The APA also cited an automotive plant in Mexico that achieved a 96% decrease in its injury severity rate through BBS
How to Implement Behavior-Based Safety at Work
Implementing a BBS program requires careful planning, commitment and ongoing evaluation. Follow these steps for a systematic approach.
1. Gain Leadership Support
The first step is to ensure that the organization’s leadership is fully committed to the BBS process. This includes providing necessary resources and actively participating in the program.
Prepare to answer all their questions about what is BBS in safety and how it can work in your specific environment.
2. Form a Steering Committee
Create a steering committee composed of representatives from all levels of the organization. This committee will oversee the implementation of the BBS program, including setting goals, planning, and monitoring progress.
3. Conduct a Baseline Assessment
Before implementing BBS, perform a baseline study to understand the current state of safety in the organization.
Review accident and incident reports, observe workplace safety behaviors and survey employees about their perceptions of safety on the job site, and whether they consider it a safe environment.
The Ultimate Guide
to Safety Inspections
Essential tools, customizable templates, and expert tactics to help you improve your inspection process
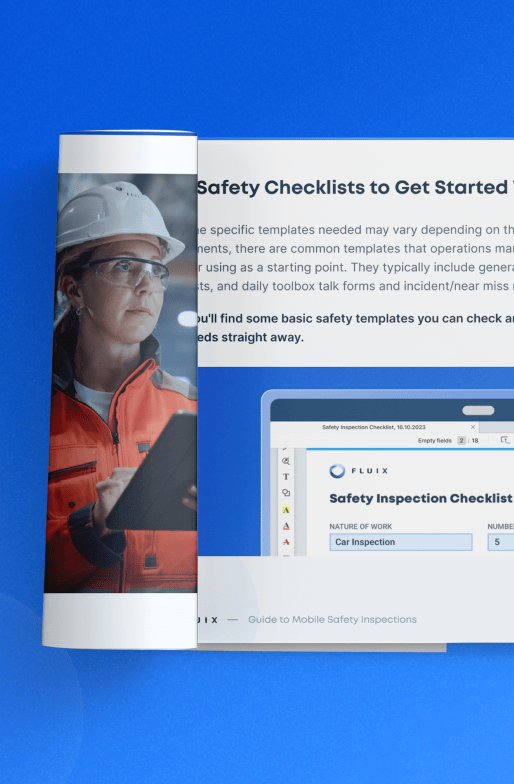
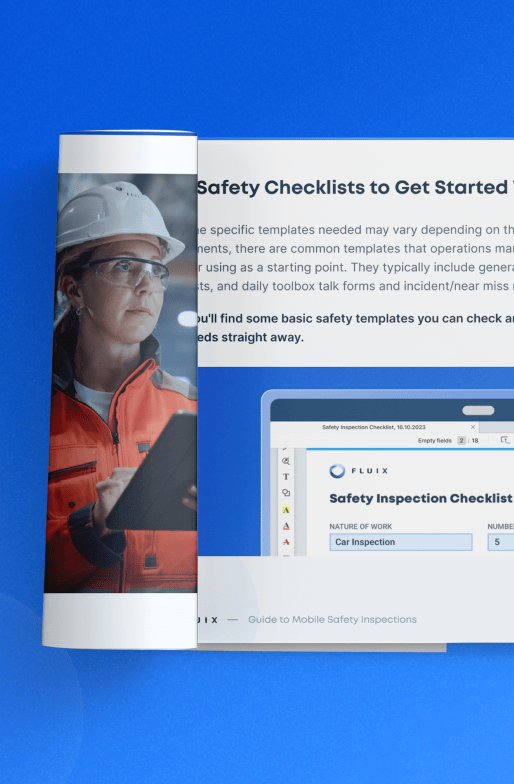
4. Train Observers
Select and train a group of employees to serve as observers. Observers should represent a cross-section of the workforce, including representation from all departments as well as both management and frontline workers.
Educate these individuals about how to conduct observations, provide feedback and record relevant data.
Read more: Read more: A safe workplace through data-driven safety practices
5. Implement Observation and Feedback
Next, observers conduct regular safety observations to identify specific behaviors that contribute to risk or negatively impact safety.
The individuals observed performing these behaviors receive feedback. The feedback sessions focus on positive reinforcement of safe behaviors and constructive discussion about unsafe behaviors observed.
6. Analyze Data and Take Action
Collect and analyze data from observations to identify trends and areas for improvement. Use this data to inform safety interventions, policy changes and create a guide to safety training.
When done effectively, BBS can dramatically lower incidents and improve overall workplace safety. A 2022 study published in the Journal of Organizational Behavioral
Management found that behavior-based safety reduced injuries by 25% during the first year of the initiative, 34% by the end of the second year and 42% after three years.
7. Communicate Openly
Using timely safety communication, keep all employees informed about the BBS process, highlighting progress made and successes achieved. Encourage ongoing worker involvement by soliciting feedback and suggestions for improving safety.
Consider introducing a system of recognition and rewards to reinforce safe behaviors. It could be as simple as verbal recognition in team meetings or as elaborate as a formal awards ceremony.
8. Sustain the Effort
Regularly assess the effectiveness of the BBS program. Analyze your available data and make adjustments as needed to optimize the company’s safety initiatives.
Ensure the longevity of the BBS program by integrating it into the organization’s safety culture. This involves continuous training, regular reviews of safety policies and procedures, and ongoing leadership support.
Launch Your Behavior-Based Safety Program with Fluix
An effective behavior-based safety initiative requires swift, accurate data collection. Fluix, workflow automation software for safety management, can connect your observers with the tools they need to quickly note the identified safety hazards, streamlining the feedback process and enhancing your improvement efforts.
And our lightweight, user-friendly app will go where your teams go for accurate, timely safety documentation.