Incident reports are essential for documenting workplace incidents and ensuring proper follow-up actions. Whether it’s a minor accident, a near-miss, or a safety hazard observation, capturing detailed information helps identify root causes and implement corrective measures.
In this guide, we’ll answer the key questions about how to write an incident report that is clear, comprehensive, and actionable, and what workplace safety software can help.
Contents:
What Is an Incident Report?
An incident report is a document that recaps information about workplace incidents, accidents, near-misses, or safety hazards.
It details injuries, property damage, security breaches, or misconduct, and also describes corrective actions.
The Purpose of an Incident Report
Employers use incident report forms to assess what happened and prevent future accidents. Reports can be springboards for actions such as:
- Safety training programs
- Risk mitigation efforts
- Strategic planning endeavors
Incident reports are also part of a safety report, with the difference that a safety report more often lists recordable incidents for a specified period. Safety managers can also use them as a base for creating toolbox talks or other safety initiatives.
Benefits of Incident Reports
Incident reports are part of an overall safety plan. They help create a safe work environment with other measures your company uses, such as instruction manuals, toolbox talks, and safety walks.
If we go into more detailed benefits, they are::
Reinforcement of the significance of the incident
Showing workers how to write an incident report reminds employees that these events matter, and that you care about their safety. It demonstrates your willingness to remediate the situation and make improvements.
Provide safety data
The information you gain from incident reports can help your company identify trends. They can show patterns, repetitive unsafe behavior, and areas that need attention. By creating and tracking incident reports using safety management software, you can accomplish a data-driven safety initiative.
Assist with compliance
Most companies have health and safety mandates to follow. Incident reports can help a company’s efforts to ensure safety compliance. They record what happened and how the company handled the incident.
By the way, managing compliance with a dedicated software like Fluix can make a big difference. Instead of manual paperwork and dispersed file locations, you have a centralized place with all your safety audits
What’s more, safety compliance documents are accessible anytime, anywhere, as long as there is an internet connection. This ensures employees can quickly access important safety information, procedures, and protocols, even when working remotely or in the field.
Read more: Read more: Audit & compliance, and 9 more features Fluix gives for safety management
How to Write an Incident Report: 5 Key Steps
Here are five foundational steps that will help you write an incident report, capturing essential information and conveying it clearly and concisely.
1. Gather the Information
It’s no rocket science that to write the report you need the information about the incident. It should cover such points:
- Where the incident happened: a specific area, such as the warehouse section or bay number
- The date and time of the incident
- The events leading up to the incident and what people did during the incident
- How many people were involved, their job titles, and their connection with the incident
- The names and contact information of witnesses
Note relevant information that may have played a role. If you were outside, did weather conditions contribute to the incident? Was there poor lighting or excessive sound in the warehouse? Did something distract the people involved? Aside from this particular report, you’ll be able to use this data for your behaviour-based safety initiatives later on.
Photos, videos, checklists, and other relevant documentation can fill in the details. FYI, with Fluix, you can gather and store all the information in one place.
The Ultimate Guide to Safety Inspections
Essential tools, customizable templates, and expert tactics to help you improve your inspection process
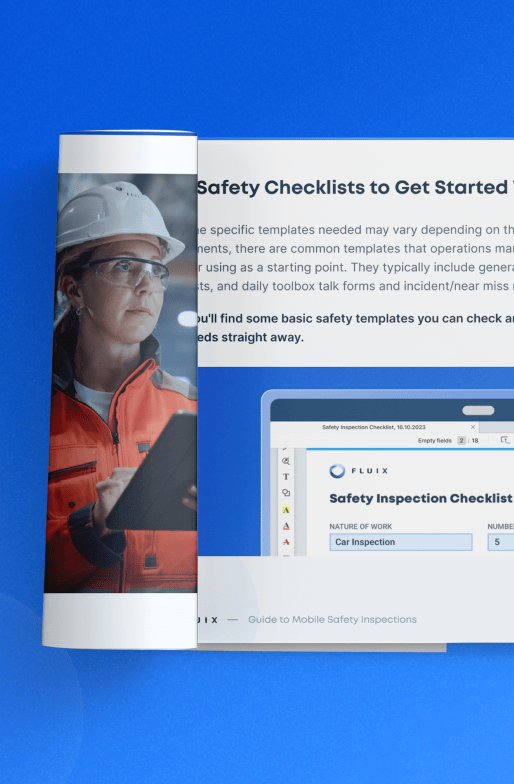
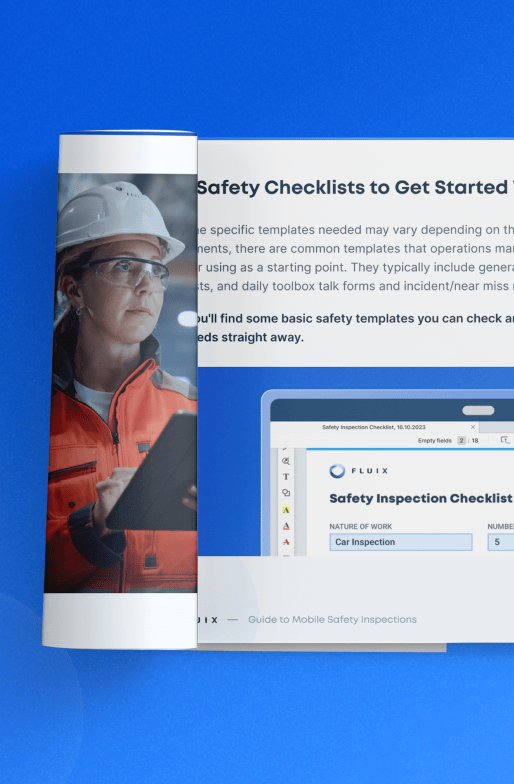
2. Put the Events in Order
The next step in determining how to write an incident report is establishing the order of events. You can begin with a summary and follow it with a detailed, step-by-step description.
And yes, this is the shortest piece of advice we’ve ever given.
3. Analyze the Incident’s Cause
Note the environment’s role in the incident: faulty equipment, safety hazards in workplace, or worker fatigue, for example. Also, record whether someone’s actions or lack of action led to the incident.
Determining what caused the incident may prevent future occurrences and lead to a safer working environment.
Be truthful and forthcoming in this section. Think about what you or others could have done differently to prevent the incident. This step demonstrates integrity and improves future safety metrics.
4. Describe Injuries or Damage
Outline any injuries resulting from the incident. Include the healthcare facility, physician, the nature of the trauma, and what type of medical treatment the person required.
No, it looks like #2 wasn’t the shortest.
5. Describe Corrective and Preventive Action
Once you have all the other steps, you can determine corrective and preventive action regarding the incident (CAPA) that is a company’s steps to recognize, correct, and prevent problems. For example, they may be regular safety walks or additional training.
Invite others involved in the incident to suggest CAPA to make the work area safer. This step is easier when you use an online incident report that everyone can access quickly.
Read more: Read more: Paper vs. digital: why it’s more secure to manage your safety documentation with software
Incident Report Best Practices
The best advice on how to write an incident report for work is record the facts accurately and maintain regular safety protocols.
Stay Objective
Stick to the facts when writing the report. Avoid including opinions or emotions.
Write the Report Immediately
Complete the report immediately after the incident, preferably within 24-48 hours. It ensures the events are fresh in your mind, helping you maintain accuracy.
Use Straightforward Language
Try to keep your report readable for investigators on any level. Avoid technical jargon when you can.
Writing an Incident Report with Safety Management Software
We at Fluix know that timely incident reports can make a difference for your safety program, and so we offer all the tools you need to write them well.
From digital templates designed for incident reporting to automated submission and reviews, Fluix ensures that incident reports are routed to the appropriate managers for approval promptly.
And with built-in integrations and reporting capabilities, you can track and analyze incident data over time, identifying trends, and areas for improvement in safety protocols.