Working in industries like construction, renewable energy, aviation, and transportation means constantly juggling safety concerns.
To help you mitigate risk effectively, we present the documents needed to ensure a safe work environment. Each document listed comes with a free downloadable template, designed for easy integration with health and safety management software.
Contents:
What Are Safety Documents?
Safety documents form the foundation of a secure workplace. They include policies, procedures, plans, and hazard guidelines designed to help control risks and communicate safety protocols.
The Importance of Health and Safety Documentation
Health and safety documentation serves as a transparent framework, acting both preemptively against potential threats and responsively following incidents.
Regular review and updates are therefore essential, covering aspects like policy assessments, risk management, and legal compliance.
Many industries still rely on paper-based safety document processes, which can make continuous updates and safety communication across teams and projects slow and error-prone.
When considering the robustness of safety documents within your organization, it’s wise to consider your workflows and processes.
Cloud-based systems, such as Fluix, digitize safety workflows and documents, making them accessible for remote teams and ensuring more accurate reporting. Fluix supports both safety document PDFs and webforms, offering flexibility in maintaining compliance.
The Ultimate Guide
to Safety Inspections
Checklists, tools, and best practices to help you meet the safety regulations for your industry and don’t risk fines
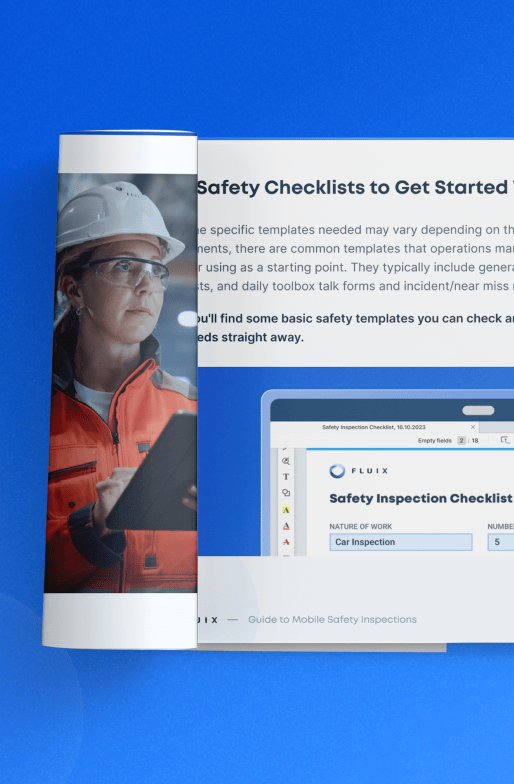
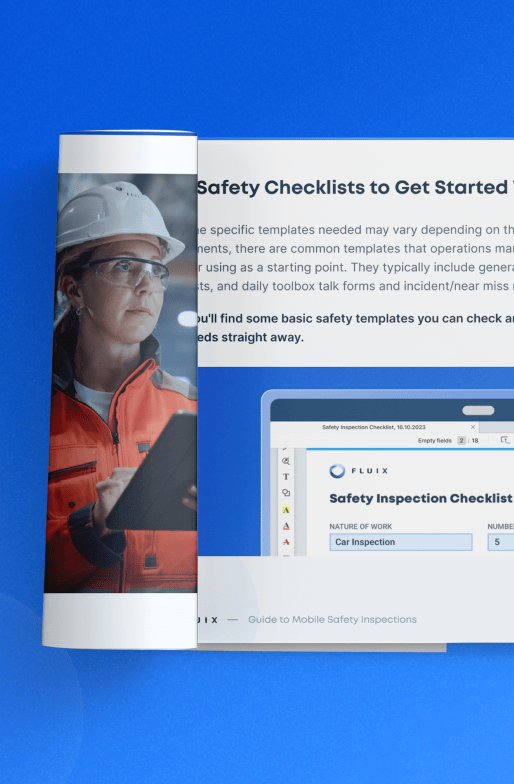
Essential Safety Documents Every Company Needs
Although each company’s documentation requirements will vary based on industry and size, these safety documents hold value across a range of high-risk sectors.
1. Near Miss Report
Near miss reports aid in recognizing protocol weaknesses, offering insights for improvement, preventing recurring unsafe scenarios, and improving workplace safety. Ultimately, their purpose is to provide crucial safety management insights.
For example, documenting incidents like repeated wrong turns in a road construction project helps identify areas for improvement.
All near miss reports can occur as a result of one or more of the following:
- Dangerous conditions
- Unsafe practices and procedures
- Human errors and oversight
- Lack of operator training
- Lack of safety awareness
- Cutting corners
- Poor communication
- Malfunctioning or hazardous tools and equipment
- Absence of a transparent system to report and record near misses
What’s Included in a Near Miss Report?
Standardized and digitized near miss forms simplify reporting by providing a consistent format. Best practices include keeping the form simple for quick completion, enabling media attachments, supporting anonymous reporting, and ensuring easy access.
A near miss report will detail:
- Date, time, and location of the incident
- Department
- Incident description
- The root cause (behavior, equipment, etc.)
- Supporting documents (photos, hazard analysis, etc.)
- Next steps and specific action items
You can download a near miss report template here for free
2. PPE Inspection Checklist
A personal protective equipment (PPE) inspection checklist is a crucial safety document for safeguarding employees in hazardous work environments.
Required by law in many countries, this checklist is designed to protect various body parts, including the head, skin, hands, and feet, as well as functions like respiration and hearing.
Its objective is to identify and address PPE issues, expedite defect correction, and prevent injuries or fatalities associated with workplace hazards.
What’s Included in a PPE Inspection Checklist?
A PPE inspection checklist typically includes sections for reporting defects and can be used in safety audits to verify that proper equipment is being used.
Templates can be tailored to industry-specific needs, serving as comprehensive reports on PPE conditions. Each template examines different hazards, with examples including:
- Eyes: Safety glasses, goggles, or face shields
- Head: Helmets and other head protection
- Ears: Earplugs or earmuffs for hearing protection
- Hands: Gloves, offering hand and arm protection
- Feet: Steel toe boots or other footwear, ensuring foot safety
- Respiratory System: Masks or breathing apparatus, based on air quality
- Full Body: Harnesses for fall protection, hazardous material suits, and similar items for overall body safety
You can download the Fluix PPE Checklist for free here
3. Risk Assessment and Method Statements
Risk Assessments and Method Statements (RAMS) provide detailed breakdowns of hazardous activities, outlining steps and risk reduction efforts.
RAMS work in harmony with the risk assessment process, forming the foundation of a proactive safety management system.
Component #1: The Risk Assessment
A risk assessment records workplace hazards, evaluates their likelihood and severity, and plans control measures to eliminate or reduce risks. This process systematically identifies potential hazards, elements causing harm, individuals or groups at risk, and effects.
Component #2: The Method Statement
Method statements expand on risk assessments by detailing hazard management, control measures, and safety precautions for specific activities. Focused on high-risk work, such as working at heights, they outline tasks, assess associated hazards, and describe control measures.
What’s Included in RAMS?
RAMS templates typically share a common structure, encompassing the following sections:
- Introduction to Project: Version details, the document preparer’s name, and method statement
- Scope of Work: Program methods, workflows, start dates, and finish dates
- Risk Assessment: Task and material-specific risks along with control measures
- Control Measures: Monitoring, supervision, and security needs, worksite safety, and personal protective equipment
- Emergency Procedures: Emergency response and evacuation protocols, including contact information
You can download a risk assessment and method statement template here for free
4. Hazard Identification Checklist
Safety officers use hazard identification checklists, also known as hazard assessment forms, to evaluate job site conditions and practices. Their primary objective is to identify potential risks and improve workplace safety. This checklist is a crucial addition to any safety documents list.
The hazard identification procedure is integrated into an organization’s Health, Safety, and Environment (HSE) management system.
What’s Included in a Hazard Identification Checklist?
When crafting your checklist, consider the specific environment and activities of your workplace. A hazard identification checklist should cover the following basic elements:
- Nature of work
- PPE
- Noise exposure
- Manual handling
- Excavation
- Working at heights
- Slip and trip hazards
- Site security and emergency preparedness
- Ambient conditions when working outdoors
- Cuts and abrasions
- Hazardous substances
- Plant and machinery
- Falling objects
- Lifting procedures
- Fire or ignition sources (hot work)
- Environmental impacts
- Decontamination of plants and equipment
- Vibrations
- Spill prevention measures
- Waste disposal
- Customers and surrounding property
- Nearby work
- Asbestos
You can download a safety hazard checklist here for free
5. Toolbox Talks Checklist
Toolbox talks are brief, informal safety meetings that complement formal training provided by the Occupational Safety and Health Administration (OSHA). They play a crucial role in safeguarding field crews and preventing accidents.
Most construction companies conduct regular toolbox talks to meet safety training requirements. These meetings refresh employees’ knowledge about hazards, safety protocols, procedures, and best practices.
If you’re new to toolbox talks, a good place to start is by reviewing the most common safety violations. According to OSHA’s 2023 data, here are the top 10:
- Fall Protection – General Requirements
- Fall Protection – Training Requirements
- Hazard Communication
- Ladders
- Scaffolding
- Powered Industrial Trucks
- Lockout/Tagout
- Respiratory Protection
- Personal Protective and Lifesaving Equipment – Eye and Face Protection
- Machine Guarding
What’s Included in Toolbox Talk Checklists?
These checklists help construction site supervisors, foremen, and managers conduct safety briefings. They details aspects such as:
- Safety topics
- Discussion points
- Attendee list
- Questions
- Feedback
You can download the Fluix Toolbox Talk Template for free here
6. Incident Report
An incident report documents workplace illnesses, injuries, near misses, and accidents. It’s crucial to complete incident reports promptly, regardless of the injury’s severity. The content required by law may vary based on federal or provincial legislation.
These reports contribute to comprehensive health and safety documentation, enhancing workplace safety practices.
What’s Included in an Incident Report?
The key components of an incident report include:
- Names of all individuals involved, including witnesses and immediate supervisors
- Specific location details, including street address and indoor facility specifics
- Activities individuals were engaged in when the incident occurred
- Factors leading to the incident and the events as they unfolded
- Descriptions of injuries resulting from the incident
- Tools or equipment used during the incident
- Identification of any hazards present
- Inclusion of photographs depicting the incident area
You can download an incident report template here for free
7. Safety Training and Orientation Checklist
Organizations use these checklists to make sure all employees, especially new hires, receive comprehensive health and safety training before starting their jobs.
These checklists methodically cover all essential safety protocols, procedures, and guidelines, ensuring adherence to regulatory standards. They are fundamental to building and maintaining a strong safety culture.
What’s Included in a Safety Training and Orientation Checklist?
This versatile checklist can be adapted to different situations, including:
- Health and Safety Questionnaires for New Employees: Assess fitness for work and understanding of best practices. Pinpoint areas within the organization that require immediate attention to improve safety standards.
- New Employee Health and Safety Checklist: Ensure procurement of necessary protective gear for employees working in specific conditions. Verify scheduling for OSHA training or site-specific safety education.
- Employee Safety Orientation Checklist: Tailor safety courses based on roles, projects, or contracts. Customize safety program elements for each orientation session.
- Safety Orientation Checklist Construction Plan: Align with client requirements for safety devices or equipment as specified in a contract. Specify mandatory training courses for onsite personnel.
- Incident Response: Capture incident details, reporting, investigation, corrective actions, and follow-up information.
- Training Course Creation: Develop new courses in response to incidents or training needs, using checklists. Ensure the formation and integration of new courses into company practices.
You can download the Fluix Safety Training and Orientation Checklist for free here
8. Lockout/Tagout Procedure Template
A lockout/tagout (LOTO) procedure is a safety protocol that ensures dangerous equipment is properly shut off during maintenance. This procedure prevents machinery from being accidentally powered on, which could cause serious injuries.
Using a LOTO procedure form helps ensure every step of this process is followed correctly, creating a safer work environment for everyone.
What’s Included in a Lockout/Tagout Procedure Template?
LOTO procedure templates typically comprise the following sections:
- Company Information: Name, logo, and other important company-related details
- Job Details: Project information for accounting and monitoring
- Table of Lockout/Tagout Steps: Basic steps with space for additional details, signatures, or initials
- LOTO Information: Machine/equipment description and details about each lockout/tagout, with photos
- Personnel: Names of individuals completing the repair and documenting the procedure, with supervisory signatures
If you work with hazardous energy, this template should be part of your safety documentation list.
You can download a lockout/tagout procedure template for free here
9. Safety Compliance Checklist
These checklists help ensure safety standards are met and inspection documents are audit-ready. They guide systematic reviews based on industry requirements, focusing on regulations from national authorities.
A comprehensive safety compliance checklist will target specific operational aspects and may include multiple sections. The purpose of the checklist will influence when and how often it is used, whether before, during, or after operations. This approach ensures that all critical safety elements are reviewed and documented.
Data-driven safety insights can inform the development and updates of these checklists.
What’s Included in a Safety Compliance Checklist?
Safety compliance checklists often cover the following key areas:
- Environment: Air quality, lighting, temperature, humidity, and noise levels
- Training: Adequacy of training on hazards, emergency equipment, job assignments, PPE, and safety procedures
- Electromechanical: Use of electrical appliances, power disconnection protocols, equipment guards, cabinet security, and lockout/tagout systems
- First Aid and Accident Reporting: Availability and condition of first aid stations, presence of first aiders, incident investigation procedures, and communication of results
- Means of Exit: Adequacy and functionality of emergency exit doors, access routes, exit markings, and emergency lighting
- Employee Facilities: Cleanliness and repair of facilities, availability of hand washing stations, and safety of cafeteria areas
- Tools and Machinery: Presence of start/stop switches, safety devices, operating procedures, lockout procedures, training on tool use, checks for defective tools, and availability of manuals
You can download the Fluix Safety Compliance Checklist here for free
Elevating Safety Excellence with Fluix
Handling safety documentation can be overwhelming, but it’s crucial to get it right. Mistakes in this area can lead to severe repercussions, including threats to workplace safety and non-compliance penalties.
Fluix eases this burden by helping you create, manage, and share health and safety documentation more smoothly than ever before. Fluix is powerful safety management software that streamlines processes and document management.
Here’s a glimpse at some of our features:
- File Assembly: Use pre-made templates and ready blocks to quickly and efficiently build your own safety forms
- Context-enrichment features: Enhance your checklists and reports with e-signatures, location stamps, and photos
- Organized paper trails: Implement automated naming conventions to streamline the organization and retrieval of your documents for audits
- Integrations: Seamlessly upload your documents to storage solutions like the Cloud, Dropbox, and SharePoint for fast and secure retrieval
- Accessibility: Retrieve your documents from anywhere, whether you’re working remotely or offline
Keep your safety documentation compliant with the help of Fluix.