When you’re working at heights, safety isn’t just a priority – it’s a lifeline. That’s where a fall protection inspection template comes in. It’s your go-to tool for ensuring harnesses, lanyards, anchors, and other critical gear are in top condition before anyone sets foot on the job.
Whether it’s a quick pre-use check or a more detailed inspection, having everything documented keeps you – and your field teams – protected.
Contents:
What Is a Fall Protection Inspection Template?
A fall protection inspection template is an essential tool for keeping your safety equipment – like harnesses, lanyards, and anchors – safe and ready to use.
By sticking to regular safety inspections, you help prevent accidents and stay compliant with safety regulations. Plus, using a checklist makes inspections faster, ensuring nothing gets overlooked.
For example, pre-use inspections give you a quick snapshot of your gear’s condition right before work begins. They’re faster than the more detailed checks you might do every few months, but still crucial for catching obvious wear and tear.
This documentation, aligned with safety protocols and enforced standards, also serves as proof of compliance when stored properly.
Keep Your Fall Protection Equipment Safe
Stay compliant and protect your teams with effective digital toolsGet Started Today with Fluix
What Is Included in a Fall Protection Equipment Inspection Form?
When you’re checking your gear for fall protection, there are four main things to look for:
- Inspector identification: Who’s doing the inspection? It’s important to log the name.
- Equipment data: Record the manufacturer and serial number of the equipment being checked.
- Equipment defects: Identify any damage or wear and tear that could affect safety.
- Readiness for service: Is the equipment safe to use, or does it need repair or replacement?
These details ensure that each piece of equipment is inspected properly and ready to go. The goal is to catch problems early – sometimes equipment might show signs of wear but is still usable for now. It’s crucial to know the difference.
Why It’s Better to Use a Digital Fall Protection Inspection Template
Now, imagine the ease of doing all your inspections digitally. Digitized safety documents don’t just save you time – they ensure nothing gets missed. They can prompt workers to complete all the required fields, flag incomplete forms, and provide real-time updates.
Let’s be honest – fall protection and paper don’t mix, especially when working at heights. Paper forms can get lost, damaged, or incomplete. Switching to digital ensures your inspections are thorough and convenient, boosting both safety and productivity.
With safety inspection solutions like Fluix, you can transform these forms into efficient workflows that standardize safety practices across your entire team. And offline access can allow workers to complete inspections remotely, even without an internet connection.
Whether you’re on-site or in a remote location, you can manage everything on your device, keeping your team safe and compliant no matter where they are.
The Ultimate Guide
to Safety Inspections
Checklists, tools, and best practices to help you meet the safety regulations for your industry and don’t risk fines
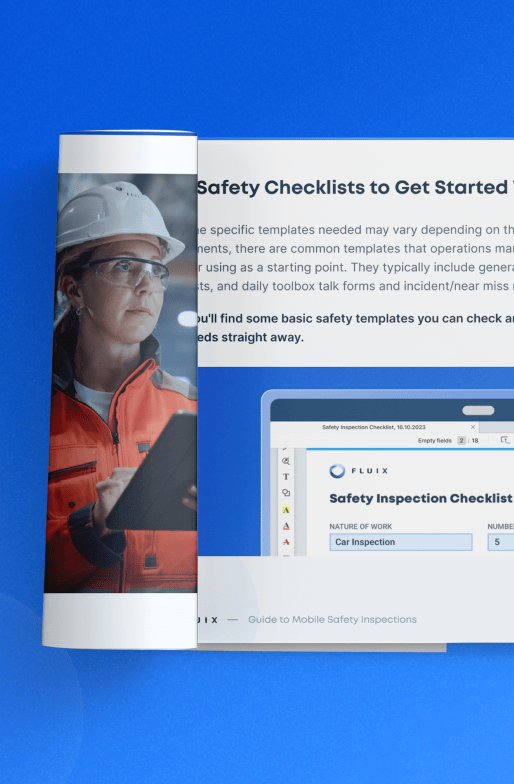
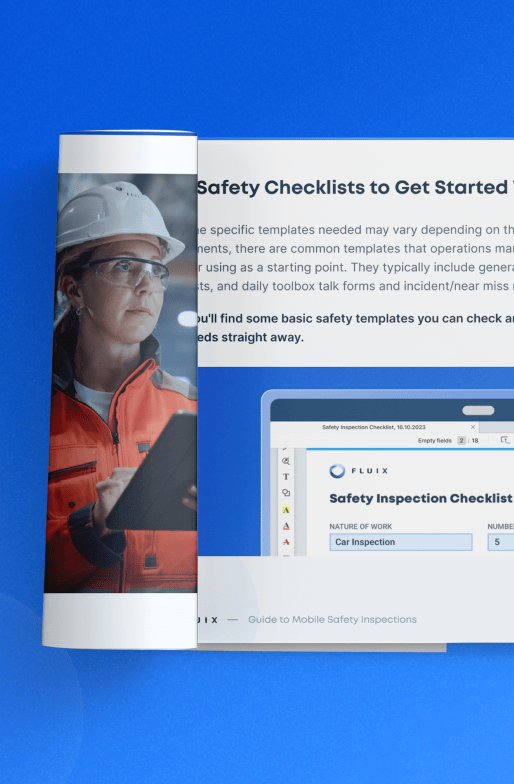
Best Practices for Creating Fall Protection Templates
Creating good safety documents isn’t always easy. Here’s how you can build a template that works for your field operations:
- Customize It for Your Crew. Tailor your template to match the type of work your team does and the gear they use. Are they inspecting harnesses, lanyards, or anchors? The more relevant the checklist, the faster and more thorough the inspection will be.
- Stick to Compliance, But Keep It Simple. Yes, you need to follow safety standards like OSHA or others, but that doesn’t mean your template has to be complex. Keep it easy to understand. Use simple checkboxes and clear prompts.
- Log the Essentials. You don’t need to overcomplicate things, but make sure your template captures the key info – like the manufacturer and serial number of each item.
- Get Visual
Your team’s out in the field inspecting gear, not sitting at a desk. Include prompts for visual checks, focusing on high-risk areas like buckles and webbing. Spell out what to look for – frayed straps, rust, worn connections – so they can spot issues quickly. - Go Digital. Digital templates, like the ones you can create in Fluix, speed up inspections, reduce errors, and make sure nothing gets missed. Plus, your team can access them remotely – even offline.
An important note is that to keep your fall protection templates truly effective, it’s important to regularly check for updates to safety regulations in your industry. Safety standards evolve, and your templates should too.
For example, if new regulations require more frequent inspections of specific equipment, like anchor points or harnesses, you’ll need to adjust your template to include those checks.
How Fluix Can Help Manage Fall Protection Checklists
Fluix is field productivity software that can simplify your entire fall protection checklist process, helping you stay compliant and keep your team safe. Here’s how:
- Ready-to-Use Template Library: Get started right away with Fluix’s library of customizable fall protection templates. No need to build from scratch – you can easily adjust templates to fit your specific needs.
- Form Builder: Want something custom? Our drag-and-drop form builder lets you create your own custom checklists in minutes. Add fields for equipment data, inspector details, or anything else your process requires.
- Mobile Accessibility: Your team can complete inspections on any mobile device, making it easy to stay on top of safety, even when they’re out in the field.
- Offline Data Collection: No signal? No problem. Fluix allows workers to fill out forms offline, and all data syncs automatically when they’re back online. This is perfect for remote sites or areas with limited connectivity.
- Photo Documentation: Want a clear visual record of your equipment? Our app lets your team add photos directly to checklists, providing extra proof that equipment is in good condition – or capturing any wear and tear.
By digitizing and automating your fall protection checklists, Fluix ensures no step gets missed, saving you time and boosting field productivity.