A safe workplace isn’t just about following rules – it’s about catching problems before they happen. Safety inspections are your best tool for this, helping you spot risks before they cause trouble.
We’ll walk you through the ins and outs of this process and share some tips to help you do them right, keeping your team safe and projects on track.
Contents:
What Is a Workplace Safety Inspection?
A workplace safety inspection is a formal on-site review of a work environment.
It’s all about examining how a workplace is set up and how things are getting done. This includes checking the layout, equipment, materials, and work practices.
During an inspection, safety inspectors spot and note down any hazards or unsafe behaviors that could put people in danger.
Their end goal is simple: to keep everyone safe by reducing risks wherever possible.
Why Are Workplace Safety Inspections Important
Safety inspections don’t always get the attention they deserve. Some might see them as just another task on the to-do list, or think their current safety measures are enough. But skipping inspections can lead to serious consequences.
Here’s why regular health and safety inspections are so valuable to your workplace:
1. Spot problems early
Regular inspections help catch workplace safety hazards before they get out of hand.
For example, you might spot a loose scaffolding plank before someone steps on it and falls. Catching these issues early can prevent accidents, and injuries, and even save lives.
2. Get to the bottom of your safety issues
Inspections do more than just point out problems – they help you understand the reasons behind them. By uncovering the root causes of safety issues, you can take targeted actions to fix them. This might mean replacing faulty equipment, changing how tasks are done, or offering more safety training to keep everyone protected.
3. Stay compliant with regulations
Conducting regular inspections ensures you’re in compliance with safety regulations, which helps you avoid fines and legal troubles. Plus, having detailed inspection reports can be a big help if you ever need to file a property insurance or liability claim.
4. Cut down on costs
Safety checks can actually save you money by catching small issues before they become big expensive problems. For example, fixing a minor equipment issue now is much cheaper than dealing with a major breakdown or accident later on.
Read More Read More 9 SafetyCulture alternatives for better safety management
Who Performs Workplace Safety Inspections
The Occupational Safety and Health Administration (OSHA) is a government agency that sets rules to keep workplaces safe in the U.S. In some fields, like construction or maritime, or when using specific equipment, OSHA requires safety inspections. But for most places, regular inspections are optional.
OSHA standards say that safety inspections should be done by “competent persons.” In other words, people who have the right skills, training, and experience to spot dangers and keep the workplace safe. But, it’s up to the employer to pick the right people for their health and safety inspection team.
Health and safety committee members or representatives are often a great choice here, especially if they’re certified. Because they’re already familiar with safety rules, they should have a good eye for spotting potential hazards.
When building your safety inspection team, it’s also a good idea to include employees from different departments. A mix of people means a more thorough inspection because each person brings their own skills and knowledge.
For example, on a wind farm, one team member might know how to spot mechanical issues with turbines, while another is skilled at finding electrical hazards.
Different Types of Workplace Safety Inspections
When it comes to keeping your workplace safe, not all inspections are created equal. Different types of inspections focus on different aspects of safety. Let’s break down the main types so you can understand what each one is about:
1. Routine Safety Inspections
Think of these as your regular check-ups. Routine safety inspections happen on a set schedule (i.e. daily, weekly, monthly) to make sure everything is in tip-top shape.
The goal here is to catch common hazards, like faulty equipment, spills, or unsafe practices, before they turn into something serious. This helps keep your workplace safe and running up to standard.
2. Risk-Based Safety Inspections
Got high-risk areas or equipment that need extra attention? That’s where risk-based safety inspections come in. These inspections focus specifically on spots that have a higher potential for danger, like hazardous materials, electrical systems, or heavy machinery.
For these inspections, you’ll need experts who know exactly what to look for in high-risk areas.
3. Unannounced Safety Inspections
Surprise! Unannounced safety inspections, also known as spot checks, happen without any warning. Why go in unannounced? Because it reveals how things are really going on a day-to-day basis. With no time to prep or clean up, inspectors get to see if safety standards are being followed all the time.
4. Pre-Operational Safety Inspections
Bringing in new equipment or starting a new process? Be sure to do a safety walkthrough first. These inspections make sure everything is safe and sound right from the start, catching potential hazards before they can cause any harm.
5. Incident Investigations
When something goes wrong, like an accident or a near miss, it’s time for an incident investigation. These inspections dig deep to find out what happened and why. Inspectors will analyze everything from equipment to employee actions to find the root cause and prevent it from happening again.
Often, these inspections are part of a larger investigation process.
6. Compliance Safety Inspections
Compliance safety inspections help keep your workplace on the right side of the law. They focus on making sure you’re meeting all legal requirements, whether those come from OSHA or regulatory bodies in other countries.
These inspections are usually more thorough, delving into details like records, permits, and safety training. They can be carried out by external agencies or internal teams who know all the regulations inside and out.
The Ultimate Guide
to Safety Inspections
Checklists, tools, and best practices to help you meet the safety regulations for your industry and don’t risk fines
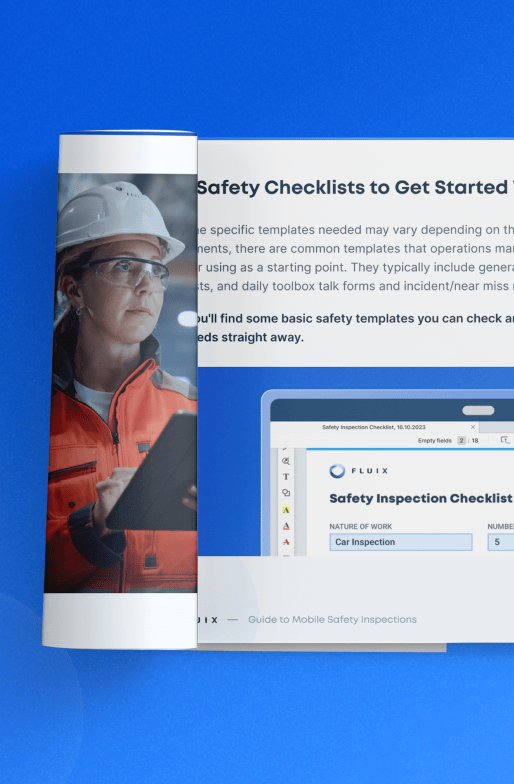
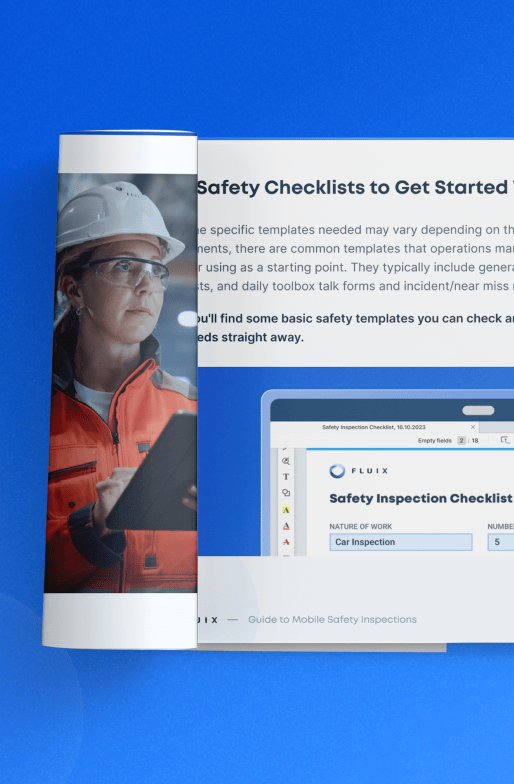
How Often to Inspect Your Workplace
There’s no simple rule for how often you should perform safety inspections – it depends on your workplace. To figure out what’s best, consider what’s happening on-site.
If your crew is working with heavy equipment or handling dangerous materials, frequent inspections are a must. High-risk activities need extra attention to prevent accidents.
You should also check out the regulations in your area. Different places have different workplace safety inspection requirements. Keeping up with these rules helps you stay compliant and avoid any legal issues.
Your safety history also plays a role. If you’ve had accidents or close calls, you’ll want to increase your inspection frequency. But if everything has been operating seamlessly, you might be able to space them out a bit more.
Doing a risk assessment is a great way to help you decide if your current inspection schedule is up to par or if you need to make some adjustments.
By keeping these points in mind, you can develop a safety inspection routine that’s just right for your organization, ensuring a safe job site for everyone.
How Do You Conduct a Workplace Safety Inspection?
To carry out a thorough review, it’s important to have a clear workplace safety inspection procedure in place. Here are the essential steps to guide you through the process:
1. Preparation
First things first, form your inspection team and establish a regular inspection schedule. If you need a refresher on these elements, scroll back up to the earlier sections of this article.
Once your team is set and your schedule is in place, take some time to review current guidelines, previous inspection reports, and any safety procedures already in place. This prep work will help you know what to focus on during the inspection and ensure you’re up-to-date with safety standards.
At this stage, you’ll also want to create a customized inspection checklist tailored to your workplace. This checklist will serve as your roadmap, covering all critical areas so nothing gets overlooked.
2. Inspection
Now it’s time to get out there and examine your workplace. With your checklist in hand, walk through your work site and keep an eye out for potential hazards. Here are some key things to look for:
- Electrical hazards
- Machinery and equipment conditions
- Personal protective equipment (PPE) compliance
- Emergency preparedness
- Material handling and storage safety
- Environmental conditions
Use an inspection form to note down everything you find. This helps keep a record of what’s been checked and is especially useful if you need to provide proof for insurance or compliance purposes.
And don’t just rely on what you see: talk to the people who work there. Ask employees about their daily tasks, how they follow safety procedures, and if they have any safety concerns or suggestions.
These conversations can reveal hidden risks or areas for improvement that you might not notice during a visual inspection. Be sure to include their feedback in your workplace safety inspection report.
3. Reporting
Once the inspection is done, it’s time to dig into the details. Start by going through all the data carefully to highlight any issues that need fixing. Look for patterns or trends that might hint at bigger problems lurking beneath the surface.
For instance, if you keep finding materials like bricks or lumber stored too close to the edges of high surfaces, that’s a serious red flag. If you notice this happening in different areas around the job site, it could mean there aren’t clear guidelines or that people aren’t following the rules for safe storage.
Spotting these kinds of trends early is key. It gives you the chance to address the root causes before they turn into bigger hazards. And if you’re not quite sure why a trend is happening or how to solve it, don’t hesitate to pull together an investigative team. A fresh set of eyes and some brainstorming can go a long way toward finding a solution.
Finding these hazards is just the beginning. The real work starts with putting together a clear safety report that outlines exactly how to tackle each issue. It should spell out what needs to be done, who’s in charge of each task and set deadlines to keep everyone on track.
A well-organized action plan can make all the difference in keeping your job site safe and preventing future problems.
4. Follow Up
After you’ve completed the inspection and put together a solid safety report, it’s time to follow up and make sure your findings don’t just gather dust. Regular check-ins are crucial to make sure that all the corrective actions are being carried out and are actually making an impact.
So, make it a habit to follow up with the teams involved, and ask for updates on their progress. Keep a record of these follow-ups and make sure to communicate your safety program actions and developments to the right people.
Improve Your Safety Inspections with the Right Software
Now that you know the steps to conducting workplace safety inspections, why not make the process even easier and more effective? With Fluix safety inspection software, you can handle all your inspection tasks in one easy-to-use app.
Going digital with Fluix means you can set up automated inspection workflows and quickly assign tasks to keep them moving along seamlessly.
Plus, you can perform inspections right from your mobile device or tablet, and instantly share results to boost communication across your team.
Fluix makes it easy to analyze your data on our app, but you can just as easily send it over to Power BI or Tableau if you’re looking for deeper insights.
And when you need to keep tabs on preventative and corrective actions, you can track it all in real-time to ensure nothing slips through the cracks.
With Fluix, you can stay on top of every detail, making your workplace safer, more compliant, and more efficient.