When your team works in fall-risk environments, their safety is in your hands. Failing to take proper precautions can easily result in tragedy.
This article will outline critical measures to prevent workplace falls and to reduce injuries should they happen. You’ll learn all about fall protection, including common hazards, essential equipment, regulations, and how safety software can support compliance.
Contents:
What Is Fall Protection?
Fall protection is a proactive approach that encompasses strategies, practices, and equipment designed to prevent falls from occurring in the workplace
Falls are the leading cause of death in the construction industry. However, this danger isn’t limited to construction sites; falls are a serious concern wherever employees work at heights, near edges, steep surfaces, or elevated platforms.
Ensuring worker safety in these environments starts with implementing comprehensive fall protection measures.
This includes recognizing and controlling hazards, following safety procedures, and using equipment like guardrails, safety nets, and personal fall restraint systems. Regular workplace safety audits play a crucial role in evaluating the effectiveness of fall protection measures. Numerous countries, including the US, have strict regulations for when and where fall protection is needed. Non-compliance can lead to substantial fines.
Fall protection is important for its own sake. It’s not about checking boxes for governmental compliance or cutting costs for insurance premiums.
Take action because you value the lives of your workers. Plus, you’ll have a serious retention problem if your workers are facing significant risk of death or injury on the job without proper precautions in place.
Common Causes of Workplace Falls
Identifying and addressing factors contributing to falls is critical to preventing them. Here are some common causes of fall injuries:
Untrained personnel: Insufficient safety training and equipment handling knowledge.
Equipment Malfunctions: Broken or poorly maintained equipment, like ladders or scaffolding.
Collapsing Structures: When buildings, ladders, or scaffolding give way.
Poor Decisions: Ignoring safety protocols or misjudging risks.
Slips and Trips: Inadequate lighting, unstable surfaces, and hazardous floor conditions.
Environmental Conditions: Bad weather, such as rain, ice, or snow.
Inadequate PPE: Failure to use appropriate fall protection equipment, like harnesses and safety lines.
Fall Protection Hierarchy
Fall protection hierarchy is a structured approach to managing fall hazards. It helps prioritize the implementation of controls to prevent falls in the workplace.
The control measures, ranked from most to least effective, are as follows:
- Elimination: The best way to prevent falls is to remove safety hazards entirely. This could mean redesigning a job or workspace so that no one needs to work at height.
- Passive Fall Protection: This method uses physical barriers to stop falls, requiring no effort from the worker. Examples include guardrails, safety nets, and hole covers. These measures are called “passive” because once set up, they work on their own.
- Active Fall Protection: These systems require employees to actively and correctly use the equipment. This includes using personal restraint systems, such as safety harnesses and lanyards, which restrict workers’ movements to prevent them from reaching areas where falls could occur.
- Fall Arrest Systems: These stop falls that have already started. They use equipment like harnesses, lanyards, and anchor points to catch falling workers.
- Administrative Controls: There are rules and procedures designed to lower fall risks. Examples include training workers, scheduling work during safer conditions, and setting up protocols. Administrative controls are considered the least effective in the hierarchy because they rely on behavior rules for safety and adherence to guidelines rather than physical measures.
Navigating Fall Protection Regulations
Fall protection requirements differ from country to country. Below, we’ve gathered the regulatory standards for the US, UK, and EU to keep you informed and compliant.
US Fall Protection Regulations
The Occupational Safety and Health Administration (OSHA) oversees all aspects of fall safety in the US.
OSHA standards for fall protection vary depending on the industry and the height at which work is performed.
Industry & Code of Federal Regulations (CFR) | OSHA Fall Protection Height Threshold | Safety Measures |
---|---|---|
General Industry (29 CFR 1910) | 4 feet or higher | Requires use of guardrails, safety nets, personal fall arrest systems, and covers for floor openings. |
Construction Industry (29 CFR 1926) | 6 feet or higher | Mandates the use of guardrails, safety nets, and personal fall arrest systems. |
Shipyards (29 CFR 1915.159) | 5 feet or higher | Includes installation of guardrails, safety nets, personal fall arrest systems, and safe use of scaffolding, ladders, and other equipment. |
OSHA also has guidelines to prevent slips, trips, and falls on walking-working surfaces (Subpart D of 29 CFR 1910). These include securing guardrails, covering floor openings, and protecting skylights.
Penalties for violating OSHA regulations are based on the severity of the violation, not the industry. Severe violations can cost up to $15,625 each. Willful or repeated violations can be fined up to $156,259 each. If violations are not fixed by the set date, additional fines of $15,625 per day can be imposed.
These figures reflect the latest OSHA penalty adjustments and may change periodically due to inflation and other factors.
UK Fall Protection Regulations
The Health and Safety Executive (HSE) enforces safety laws in the UK, including those related to fall protection.
Regulations | Details | Safety Measures |
---|---|---|
Work at Height Regulations 2005 | Covers all work at height with risk of injury | Conduct risk assessments and implement controls. Ensure work is planned, supervised, and performed by competent individuals. Use equipment or measures to prevent falls, and minimize fall distance and consequences. Provide training, and appropriate equipment. |
Personal Protective Equipment at Work Regulations 1992 | Requires suitable PPE for health or safety risks, including falls | Distribute PPE, such as harnesses and helmets, maintain in good condition, and train employees on proper use. |
Construction (Design and Management) Regulations 2015 | Ensures health and safety in construction projects, including fall prevention | Plan and manage safety in projects. Appoint safety managers. Identify and mitigate fall hazards. |
Companies that don’t keep up with compliance with safety laws in the UK can face unlimited fines, and in severe cases, company executives or managers could be jailed.
The Ultimate Guide
to Safety Inspections
Checklists, tools, and best practices to help you meet the safety regulations for your industry
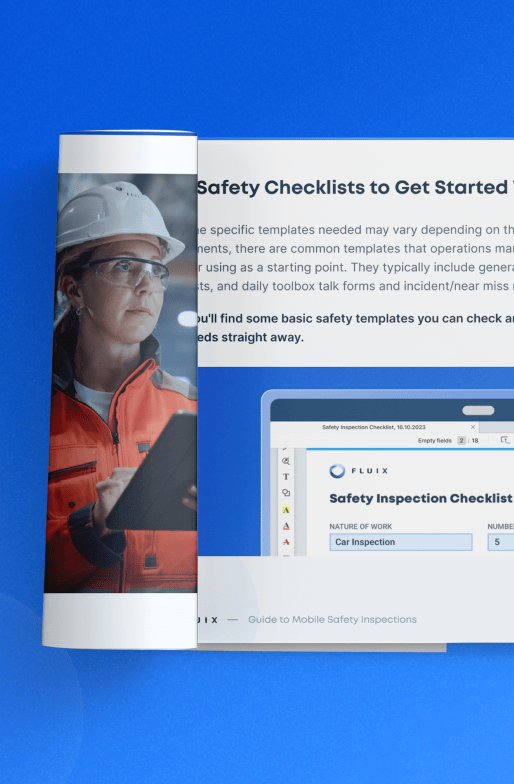
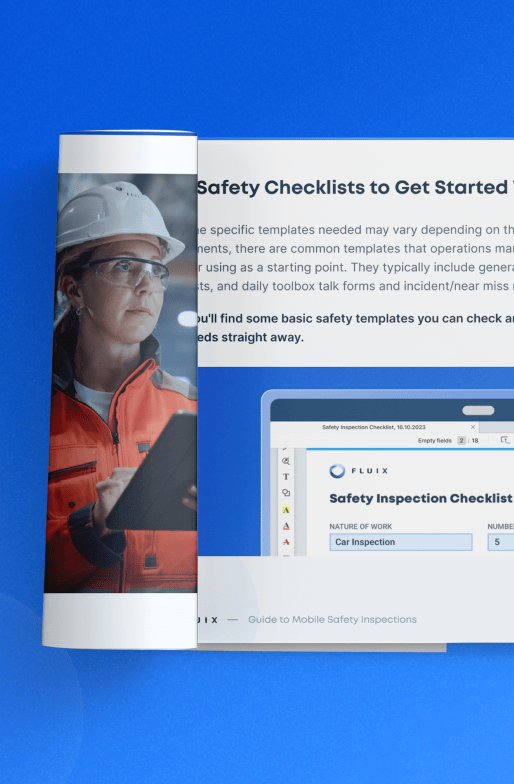
EU Fall Protection Regulations
In the EU, fall protection is managed by the European Agency for Safety and Health at Work (EU-OSHA). This agency provides the overall framework, resources, and guidelines for workplace safety in the EU. However, enforcement of these directives is the responsibility of national authorities in each member state.
Directives | Details | Safety Measures |
---|---|---|
2009/104/EC | Minimum safety and health standards for work equipment, including temporary work at height | Provide suitable, well-maintained equipment, and worker training. |
92/57/EEC | Safety and health requirements for temporary or mobile construction sites | Create a safety plan. Use scaffolding, guardrails, and other protective measures. |
89/656/EEC | Minimum requirements for PPE | Distribute appropriate PPE, including harnesses and lanyards, and ensure regular equipment maintenance. |
Note: Directive 2001/45/EC has been consolidated into Directive 2009/104/EC.
Fines for non-compliance vary by country within the EU. Penalties can include significant fines and restrictions on business operations. Severe violations can lead to criminal charges and substantial financial penalties.
Did you know that safety management systems can help you manage and adhere to your specific regulatory requirements?
Essential Fall Protection Equipment
To ensure regulatory compliance and safe working conditions, it’s important to consider many factors, including gear.
Here are three critical equipment considerations:
- Each piece of fall protection gear should fit the worker using it. For example, a harness that fits someone weighing 160 pounds won’t work for someone weighing 230 pounds. Equipment like harnesses needs to be sized and adjusted for each worker’s height and weight to ensure proper support in case of a fall.
- Personal protective equipment, such as safety nets and lines, should be inspected regularly before each use. Check for any signs of wear, damage, or malfunction. Keep detailed inspection records.
- Regular maintenance, including cleaning, repairing, or replacing parts as needed, is also essential. Both inspection and maintenance procedures help prevent equipment failures that could result in accidents or injuries.
The ABCDs of Fall Protection
If you’ve ever heard the term ABCD mentioned at your work site or office, you might wonder how it relates to safety. This acronym represents the four fundamental components of fall protection systems.
Here’s a detailed look at each component:
A is for Anchorage
Anchorage is the secure point to attach safety equipment like lifelines or lanyards. Think of it as a strong anchor point that holds you if you fall. It can be a beam, post, or other sturdy structure. For anchorage to be adequate, it must be able to support a heavy load and meet OSHA safety standards.
B is for Body Harness
The body harness is what workers wear. It spreads out the force of a fall to protect the body. It’s essential that it is used as the manufacturer recommends.
C is for Connecting Device
The connecting device links the body harness to the anchorage. These include lanyards and self-retracting lifelines. They should always be used according to guidelines.
D is for Descent and Rescue
Descent and rescue is the ability to safely lower a worker who has fallen and is suspended in the air. This process requires a well-defined rescue plan and ensuring that all equipment is ready and functional.
Practical Steps to Improve Fall Protection
Improving fall protection involves a combination of thorough training, regular inspections, and careful planning. Here’s what this could look like in practice:
Step 1: Training
Hazard Recognition and Risk Assessment
Initial Training: Start with an introductory course covering the basics of fall hazards, including examples of common scenarios and case studies.
Interactive Sessions: Use immersive tools such as virtual reality (VR) to help workers recognize fall hazards in a controlled environment.
Accessible Training Materials
Multilingual Resources: Provide training materials in multiple languages spoken by your workforce. Use visual aids, infographics, and simple language to ensure comprehension.
Digital Access: Make training resources available online for easy access anytime, anywhere.
Hands-On Demonstrations
Practical Drills: Regularly practice setting up and using fall protection equipment. Ensure workers practice with the actual equipment they’ll use on the job.
Regular Refresher Courses
Quarterly Updates: Implement refresher courses to cover new equipment, updated protocols, and lessons learned from recent incidents.
Feedback Sessions: Encourage workers to discuss their fall protection training challenges to improve safety in the workplace.
Evaluation and Documentation
Competency Tests: Workers should demonstrate their ability to use fall protection PPE correctly before being allowed to work at heights or in other hazardous environments.
Recordkeeping: Maintain detailed documentation of each worker’s training progress and proficiency evaluations.
Step 2: Inspection
Routine Inspections
Daily Checks: Implement pre-shift inspections of work areas, with an eye for potential fall hazards.
Worker Participation: Encourage employees to perform quick visual inspections of their gear before use and to report any issues they spot.
Detailed Records:
Inspection Logs: Safety managers should use digital documents for quick and easy access.. Log entries should include photos and detailed notes if any hazards or problems are identified.
Step 3: Planning
Comprehensive Fall Protection Plan
Site-Specific Plans: Create fall protection plans tailored to each worksite, considering unique hazards and specific tasks.
Emergency Response Plan
Rescue Training: Train a team specifically for emergency operations. Ensure they are familiar with equipment and procedures for a quick rescue response.
Mock Drills: Conduct regular emergency drills to practice and refine response procedures.
Stay Informed
Regulatory Updates: Assign a team member to monitor safety regulation and industry standard changes. Share updates with the entire team.
Industry Conferences: Participate in safety conferences and workshops to stay current with best practices and emerging technologies.
Enhance Your Fall Protection Compliance with Fluix
Worker safety in fall-risk environments involves coordinating many moving parts—training, inspections, and recordkeeping to name a few. Software for safety management streamlines and organizes safety processes, making management more efficient and ensuring no detail is overlooked.
Fluix is a user-friendly platform designed to help companies optimize and automate their workflows and documentation. Its mobile accessibility makes it particularly suitable for field teams.
With Fluix, your workers can:
- Submit safety reports remotely
- Edit critical safety documents on the go
- Leave voice comments on inspection documents
- Use Apple Shortcuts to keep hands free while working at height
By organizing and automating fall protection documentation, Fluix enables seamless process management.
Fluix is not just a tool for regulatory compliance; it is a comprehensive solution that enhances safety, operational efficiency, and overall project success.