The maritime industry obliges shipping companies to comply with a lot of regulations, classification requirements, conventions, and codes regulating fleet driver safety and fleet maintenance. To name a few,
- International Safety Management (ISM) Code
- International Ship and Port Facility Security (ISPS) Code
- International Maritime Dangerous Goods (IMDG) Code
- Casualty Investigation Code
- The International Convention for the Prevention of Pollution from Ships (MARPOL) Certification, and Watchkeeping for Seafarers (STCW)
- STCW (Seafarer’s training, certification and Watchkeeping) Code
To be compliant, companies should implement procedures and checklists that will ensure safe operation onboard and prevent hazardous situations. Part of SMS, maritime checklists help standardize and unify procedures, and ensure they’re being followed as intended.
The problem is that although the maritime industry is making its way to modernization, the pace is slow when it comes to document management. Most checklists still exist in paper format, are kept in folders and stored in office archives. Crews lack access to the latest versions, which are released after the vessel sets sail. Filling a paper checklist on a vessel in heavy weather is also challenging.
Benefits of Checklists
Mobile checklists and fleet safety templates can improve safety management programs, replace paper forms, reports and logs. For vessels crews, they are easier to access, fill in, sign in, and send for review. You can add to checklists images, geolocation, barcodes, and time stamps, giving more evidence for the jobsite inspection.
For office teams, they reduce administrative work and simplify reviewing. The completed checklists are kept in a single storage, centralizing data from numerous sources.
1. Conduct mobile inspections
You can assign checklists for daily inspections, job hazard detection, crew inspections and more. It’s possible to ensure all critical info in checklists is entered by making the corresponding fields required. A crew officer won’t be able to complete a checklist without filling them in.
If you use software for fleet management like Fluix you can set notifications that say crane operators will see on their mobile device or in email. This will prompt them to complete the chelists in time, ensuring accountability.
To reflect the inspection, take a photo of the jobsite and add it to the checklist. Aside from giving proof to the inspection, this will keep the onshore teams can’t be onsite themselves updated.
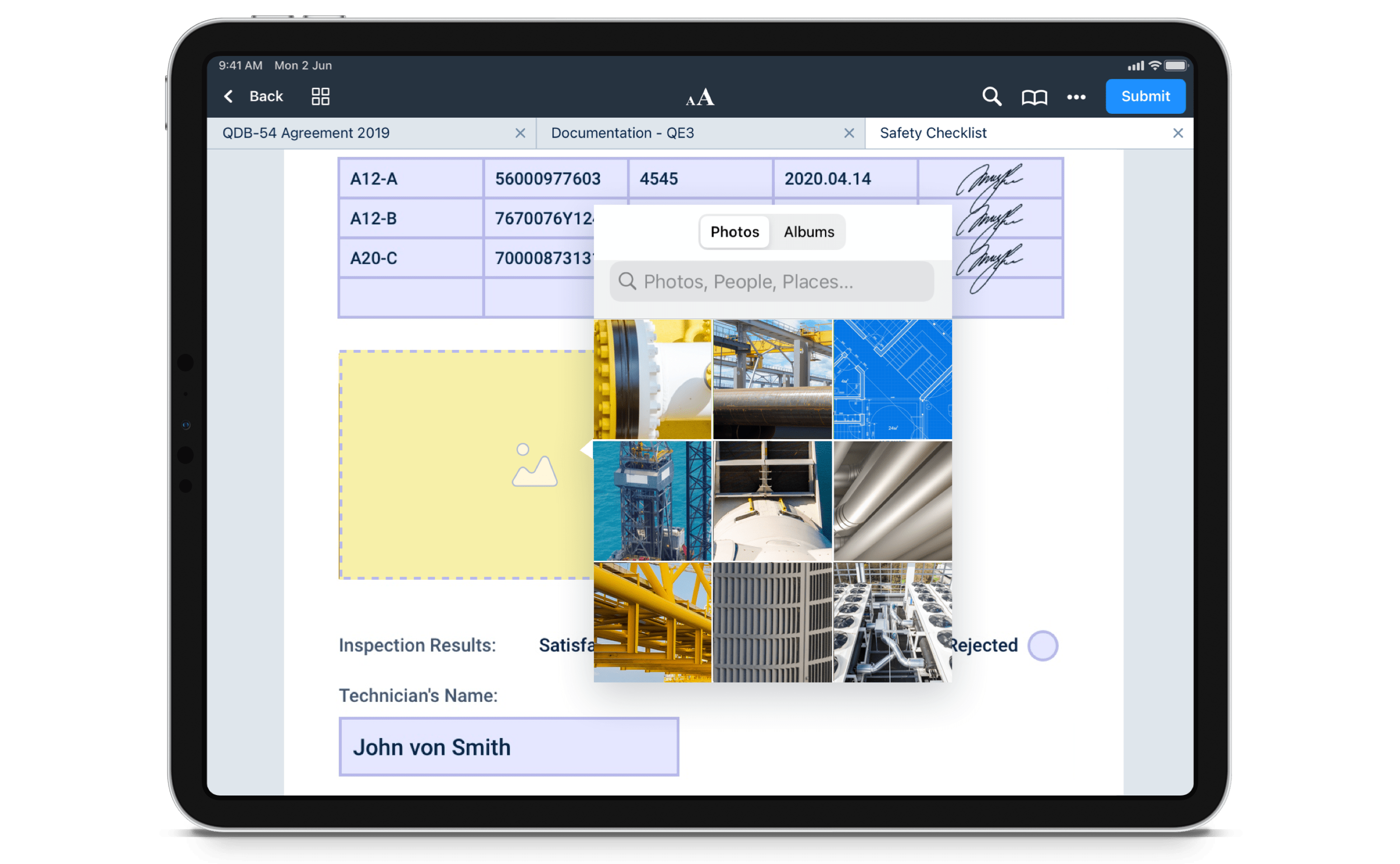
2. Ensure compliance with regulations
Maritime international regulations do improve safety but also create an extra load on documentary management. With checklists, you can create a digital recording of all documents required to comply with legal requirements of ISM, ISPS, IMDG, and more.
The approved and signed versions of the checklists are kept in a cloud-based storage, meaning they’re always available for the shore office or onboard crews.
Moreover, digital checklists promote accountability. It’s always possible to check the status of each checklist and see who was responsible for a particular inspection.
Audit & Compliance for Maritime Safety
How checklists and automated workflows help manage documentation on compliance to the company’s SMS and safety and environmental regulations
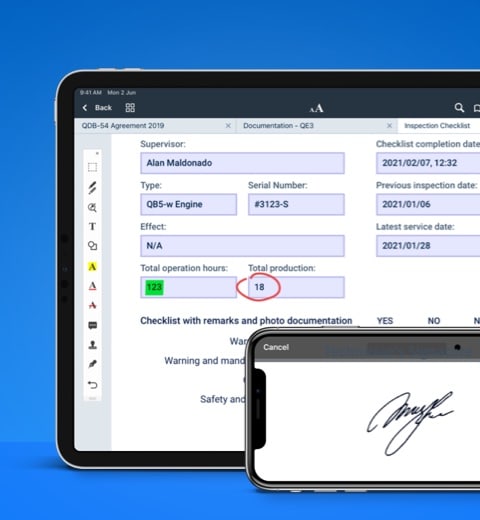
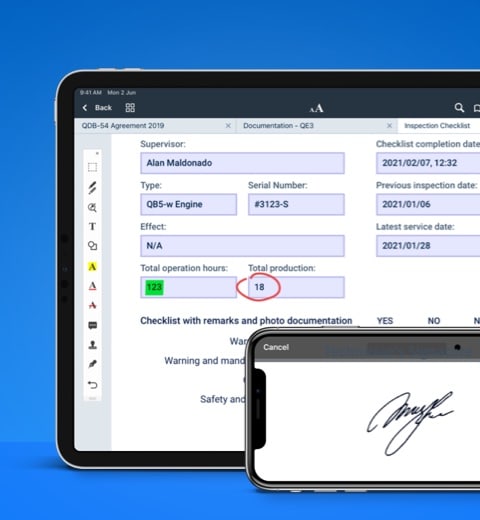
3. Improve communication between ship and shore
The shoreside team, safety directors, fleet managers or dispatchers can review completed checklists in real-time. They can see when the inspection is in progress or completed and who is responsible for each inspection.
For example, the dispatcher assigns the checklist, the operator completes the inspection and fills in the checklist, the manager reviews it and sends it to the safety director for overall analysis.
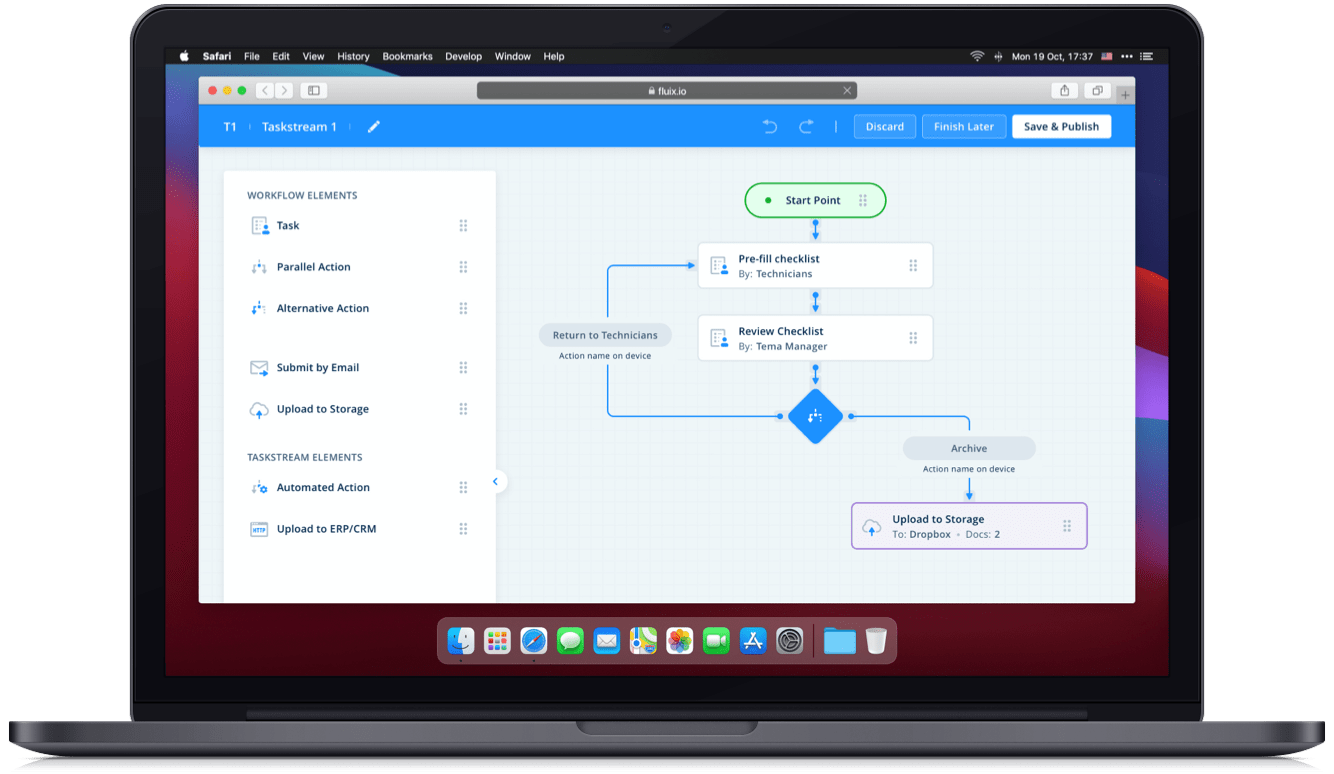
If any defect or potential hazard is identified during the inspection, the manager doesn’t need to fill in additional paper forms, drive them to the office, make calls or write emails. They can communicate deficiencies in the comments to the checklists, and they will become visible to everyone participating in the process.
If the detected deficiencies require additional maintenance efforts or repair, the checklists can be attached as evidence when creating work orders or scheduling maintenance. Again, you don’t need to fill extra forms, print, physically distribute to all parties involved (which may be a lot), and communicate the issues via disparate channels.
How Fluix Can Help the Maritime Industry
Fluix is a web app that automates processes related to fleet vehicle safety and fleet maintenance. It offers mobile checklists and automated workflows that route them between everyone involved in the process.
- Fill in checklists on a mobile device, adding images, geolocation and date. You can do it in the offline mode.
- Send them for review and eSignature.
- Send the signed checklist to the safety director or office team.
- Extract data from the checklists into a spreadsheet, or export it to a BI tool for analysis.
- Upload the checklist to a cloud-based storage and control access to it.
All these steps are automated within a workflow. You don’t do them manually but only watch over the progress and make the adjustments if needed.