Ever changing regulations of hazardous substances and a complex global trade network mean that dangerous chemicals must be listed, handled, and disposed of safely – and in ways that are standardized around the world. Safety data sheets are essential to this requirement.
In this article, we will take a look at how to create and manage safety data sheets, when you need to use them, and how industry-specific work safety software can help.
What Is a Safety Data Sheet?
A safety data sheet (SDS) is a document that gives you all the essential info about a chemical substance or mixture. It covers properties, hazards, safe handling practices, and emergency control measures.
Safety data sheets are one of the essential documents for safety for high-risk businesses that need to manage safety compliance around hazardous chemicals and products. They’re designed for professionals rather than the general public.
Types of a Safety Data Sheet
Hazards in the workplace come in different forms and require different SDSs for proper documentation and management.
There are two main types of safety data sheets:
- Material safety data sheet (MSDS)
- Product safety data sheet (PSDS)
Material Safety Data Sheets
Material safety data sheets (also referred to as safety data sheets for chemicals or chemical safety data sheets) provide comprehensive information about the physical properties and hazards of dangerous chemical substances. They include guidelines for handling spills and other safety practices.
MSDSs are created for materials such as dangerous reactants, poisonous or infectious materials, oxidizing agents, compressed gasses, flammable and combustible liquids, and corrosive substances.
These sheets are mandated by the Occupational Safety and Health Administration (OSHA) to ensure workplace safety and compliance. Manufacturers and importers are required to obtain an MSDS for each hazardous chemical they produce or import.
Additionally, distributors must ensure that their customers receive a copy of these MSDS sheets, ensuring the safe and informed use of these chemicals throughout the supply chain.
Product Safety Data Sheets
PSDSs provide safety information about a broader range of products, not just chemicals. This can include materials, devices, or other goods that may have associated hazards.
Product safety data sheets may be used to comply with industry-specific regulations and standards that go beyond chemical safety, encompassing broader product safety requirements.
The differences between MSDCs and PSDSs can seem subtle, and at times overlap. The older MSDS formats varied from source to source within a country, but newer SDS format is internationally standardized.
Chemical and product safety data sheets together comprise a legally compliant and complete ecosystem of safety related protocols, for professionals who handle hazardous chemicals and products.
Read More Read More Paper vs. digital: Why it’s more secure to manage your safety documentation with software
Safety Data Sheet Regulations Across Different Regions
As you might expect, SDS must be compliant in many ways, and are regulated by different bodies in different global territories.
A safety data sheet is mandatory for a UK business to comply with Restriction, Evaluation, Authorization and Restriction of Chemicals (REACH). The Control of Substances Hazardous to Health (COSHH) Regulations govern the use of hazardous substances in the workplace in the UK and require an assessment of the use of a substance.
In the U.S., the Occupational Safety and Health Administration requires that SDS be readily available to all employees for potentially harmful substances handled in the workplace under the Hazard Communication Standard.
In Canada, the program known as the Workplace Hazardous Materials Information System (WHMIS) establishes the requirements for SDSs in workplaces and is administered federally by Health Canada under the Hazardous Products Act, Part II, and the Controlled Products Regulations.
In the EU, safety data sheets have been made an integral part of the system of Regulation (EC) No 1907/2006 (REACH). The original requirements of REACH for SDSs have been further adapted to take into account the rules for SDS of the Global Harmonized System (GHS).
What Should Be Included in a Safety Data Sheet
Different regulatory bodies may have specific requirements for the content and structure of these sheets and related protocols for safety in the workplace.
Below, we’ll outline the 16-section safety data sheet format that is part of the Globally Harmonized System of Classification and Labeling of Chemicals (GHS).
It’s developed by the United Nations to create a universal standard for chemical safety, and includes the following safety data sheet sections:
1. Identification of the substance/mixture and of the company/undertaking
A description of the chemical product or mixture. Include its name, area of use, what it should not be used for, and the name and contact details of the manufacturer and supplier. If a chemical product is hazardous, include the Unique Formula Identifier (UFI) in this section.
2. Hazards identification
Detail the hazards the chemicals could pose to staff and the environment. Pictograms relating to CLP (if you’re in Europe), OSHA (if you are in the United States), and WHMIS (if you are in Canada), must be included along with a hazard classification. It should also include hazard and precautionary statements, and a description of hazards not classified.
3. Composition/information on ingredients
Highlight the hazardous ingredients of the mixture or chemical product in detail.
4. First aid measures
Detail first-aid measures that must be taken if someone is exposed to a hazardous chemical product.
5. Firefighting measures
Indicate fire fighting measures that pertain to the specific chemical product. State whether the substance is flammable or not, and under what conditions.
6. Accidental release measures
State exactly what to do if there is an accident on site (a chemical spill or leak). Detail how to clean it up, what protective clothing is required, and how to prevent this from happening again.
7. Handling and storage
State what handling and storage procedures and requirements are needed to mitigate risks that pertain to this chemical product. Mention storage conditions (such as temperature etc), and how to use the product correctly.
8. Exposure controls/personal protection
PPE required and exposure control limits must be detailed clearly in this section.
The Ultimate Guide
to Safety Inspections
Checklists, tools, and best practices to help you meet the safety regulations for your industry
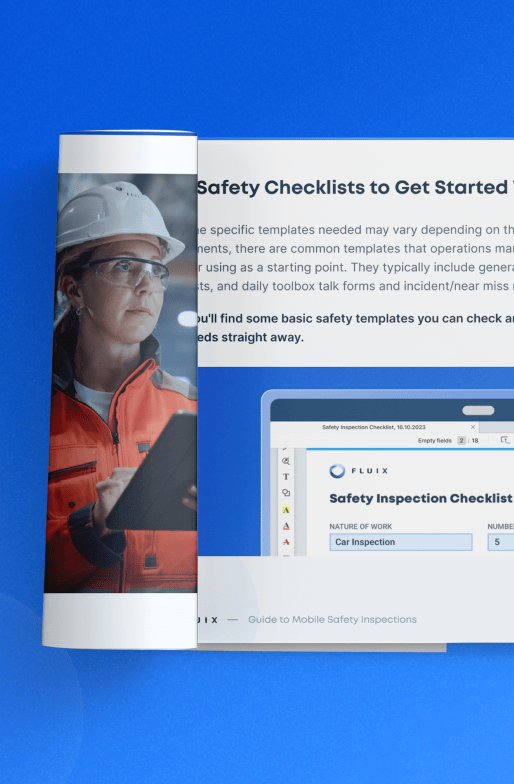
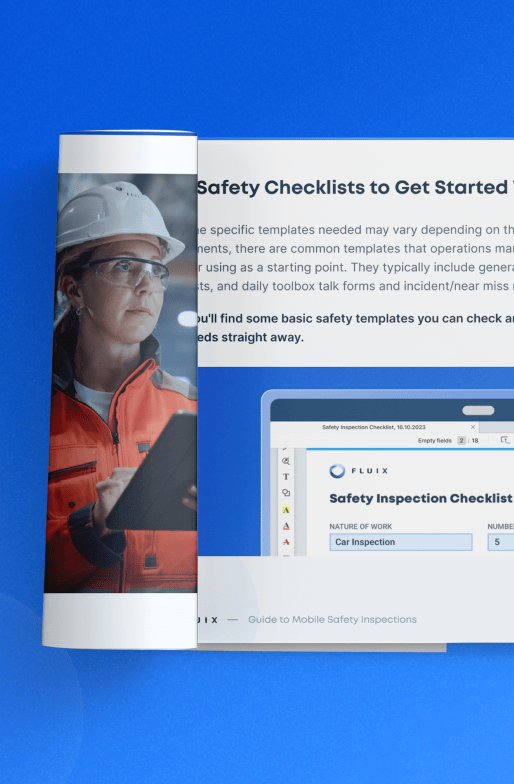
9. Physical and chemical properties
Document the physical and chemical properties of the substance – things like boiling and freezing points, specific gravity, explosion data, autoignition temperature, and more.
10. Stability and reactivity
Explain the stability and reactivity of the substance in this section. Is the chemical stable or not and if not, under what conditions? Is it incompatible with other substances? If so, which? All this must be detailed here. State whether it is reactive, how it will react, and under what conditions this may occur.
11. Toxicological information
Write down the effects of possible acute and chronic exposure to the substance. Include levels of toxicity, teratogenicity, mutagenicity, carcinogenicity, and all related exposure risks.
12. Ecological information (non-mandatory)
Explain exactly what happens if the substance is released into the environment.
13. Disposal considerations (non-mandatory)
Write about how to dispose of the chemical product properly. What protective equipment should be worn during the disposal? Is the waste classified as hazardous? List these details here.
14. Transport information (non-mandatory)
State whether the substance can be dangerous during transportation, and what steps to take to mitigate this risk. If applicable, document the dangerous good classification, including the UN number, hazard class, and packaging group.
15. Regulatory information (non-mandatory)
Detail all substance compliance details pertaining to the regulating body in your region here. This may include regulations to protect employees or the environment, and/or if the substance is subject to any restrictions.
16. Other information
Document things that people must know when using this chemical product – advice on training, when the safety data sheet will need updating, and an explanation of abbreviations used in the SDS etc.
How to Write a Safety Data Sheet
To communicate safety and stay compliant, SDS should contain all of the above sections with the requirements of each section detailed.
Using clear and concise language, including common names and CAS numbers, and standardized formats will help you make the sheets accessible and easy to read.
Here are some other useful practices to apply:
- List all ingredients, their concentrations, and relevant safety information.
- Use clear and consistent headings for each SDS section.
- Ensure the SDS is regularly updated to reflect the most current safety information and regulatory changes.
- Implement a regular review process to catch any errors or outdated information and audit safety.
- Make sure that all labeling requirements are met, including hazard symbols, signal words, and precautionary statements.
Best Practices for Managing a Safety Data Sheet
Effective management of Safety Data Sheets (SDS) is crucial for creating a safety culture and staying compliant in industries such as construction, energy, and aviation.
Here are the best practices for SDS authoring, storing, and overall management:
1. Standardize safety data sheets authoring
Utilize standardized templates to ensure consistency and compliance. Establish clear guidelines and protocols for authoring SDS to maintain uniformity across all documents.
Why is this important? Consistency helps in avoiding misinterpretations that can lead to safety hazards.
2. Centralize safety data sheets storing
Store all SDS documents in a secure and organized manner. Make sure to set appropriate access controls so only authorized personnel can edit SDS, while making them viewable to all relevant employees. Remember, easy access to accurate information can prevent accidents.
3. Do regular reviews
Conduct regular reviews (e.g., annually) to ensure all SDS are up-to-date. Stay informed about regulatory changes that may affect your SDS and update them accordingly. Regular reviews help catch any errors or outdated information before they become a problem.
4. Train your employees
Conduct regular safety training sessions on how to read, interpret, and use SDS. Provide clear, easy-to-understand guides and materials on SDS usage and safety protocols. It shouldn’t be a surprise that well-trained employees are less likely to make mistakes that could lead to safety incidents.
5. Track compliance
Keep records of who has accessed and acknowledged the SDS to ensure compliance. Maintain detailed logs of all updates and accesses to the SDS for regulatory compliance and internal reviews.
6. Invest in the right software
Implement software solutions to streamline SDS management, ensuring that your documentation is accurate, compliant, and easily accessible. This helps automate workflows, track changes, and maintain a high standard of safety across your organization. Additionally, the right software can save time and reduce human error.
Streamlining SDS with Fluix
Managing safety data sheets manually can be time-consuming, among other things, and this is where automation software like Fluix comes in handy.
Fluix is a digital platform that offers extensive functionally for safety management, including:
- Centralized document repository where all SDS can be securely stored, easily accessed, and authored.
- Automation of document workflows, including the creation, review, approval, and distribution of SDS.
- Notifications ensure that any changes in regulations or updates to SDS are promptly communicated to all relevant personnel and authored.
- Audit trails, version control, and reporting help businesses stay compliant with regulatory requirements.
- Accessibility and collaboration among team members, regardless of their location.
- Secure data storage with robust encryption and security measures.
By knowing the related requirements and following the best practices we’ve outlined in this article, you can create a safer work environment and ensure your SDS management is both effective and compliant.