Each year, an estimated 2.78 million workers die from occupational accidents and work-related diseases, while an additional 374 million workers suffer from non-fatal occupational accidents.
Keeping people safe from occupational hazards is critical, and safety compliance management is central to this endeavor.
In this article, we’ll take a deep dive into compliance safety, its applications and examples. We’ll also explore how tried and tested workplace safety software helps HSE and compliance go hand in hand in highly regulated industries.
Contents:
What Is Safety Compliance?
Safety compliance is the continuing process of meeting regulations that ensure the occupational health and safety of employees, reducing hazards and risks within a workplace.
Rules for safety compliance are set by the corresponding governmental and industry bodies based on evidence, research and industry practices.
Why Is Safety Compliance Important?
The main aim of safety compliance management is to keep workers safe. But of course, safety regulations must be adhered to for legal reasons, too.
Failure to comply with health and safety regulations can result in injuries. For example, if a contractor falls off a faulty or missing guard rail on the platform of a lifter, such injuries can lead to employee sick leave, lawsuits, penalties, and/or substantial payouts for injured employees.
Health and safety regulators can impose significant fines on businesses that violate safety regulations (or even have documents for managing safety filled out incorrectly). So this is something you always want to get right.
Effective safety compliance can also:
- Improve morale and productivity – workers and teams who feel safeguarded, feel valued. Better morale often means increased productivity.
- Reduce the risk of worker compensation payout – fewer workplace injuries means fewer health and safety compliance related payouts claimed successfully.
- Reduce healthcare costs – if related to work-related illness or accident in the workplace, often these costs are borne by employers.
- Avoid penalties and litigation fees – claims can be very expensive to challenge legally, and penalties imposed following successful claims can be even more expensive.
- Improve brand image – you become known for your great health and safety record and treatment of workers. Word gets around, your reputation benefits – so does your brand.
Recognition of the importance of proactive compliance tactics is an asset to any business – especially in highly regulated industries such as renewable energy, aviation and construction.
Improve your safety management with digital audit trails in Fluix
Regulatory Bodies Overseeing Safety Compliance
As you might expect, safety compliance management is regulated by different organizations in different countries. These bodies all mandate slightly different standards, and can impose different metrics to track safety but they all exist to achieve a common goal: no accidents in the workplace.
- In the USA, safety compliance is largely controlled by the Occupational Safety and Health Administration (OSHA) and the Mine Safety and Health Administration (MSHA). These entities regulate general industry, agriculture, construction, maritime, and mining. Farmers with family operated businesses, self-employed people, and public-sector workers are regulated by other entities with similar policies.
- In Canada, there are 10 provincial, three territorial, and one federal jurisdictions for Occupational Health and Safety regulations. Each jurisdiction has its own legislation that governs general rights and responsibilities of the employer, the supervisor, and the worker.
- In the UK, health and safety compliance is regulated by the Health and Safety Executive (HSE), and by The European Agency for Safety and Health (EU-OSHA). The EU-OSHA consists of the European Free Trade Association (EFTA) states, candidates, and potential candidate countries (European Agency for Safety and Health at Work, 2018).
Other regions have their own specific regulatory frameworks and authorities responsible for reporting safety.
To determine which ones to follow for your industry, clearly identify specific activities your business engages in, research national agencies, check industry-specific bodies, and consider consulting trade associations in your sector.
Safety Compliance Examples
How does your business stack-up when it comes to safety compliance and best practices? It’s always useful to see how we can improve, right?
Take a look at the following good and bad scenarios which give the term ‘safety compliance’ meaning, because we can see the consequences of negligence or no behavior-based safety established.
Good Safety Compliance Example
Scenario: A manufacturing company with a high risk of occupational hazards such as machinery accidents and chemical exposures.
The company undertakes the following compliance safety measures:
- Risk Assessment: Regular and thorough risk assessments are conducted to identify and mitigate potential hazards.
- Training: All employees receive safety training specific to their roles and the equipment they use, including refresher courses annually or after any significant process change.
- Equipment and Safety Gear: The company provides all necessary personal protective equipment (PPE), such as gloves, helmets, and safety goggles, and ensures all machinery is up to date with the latest safety features.
- Emergency Preparedness: Clearly marked and unobstructed emergency exits, regularly tested emergency alarms, and well-equipped first aid kits are available. Drills are conducted semi-annually.
- Employee Engagement: Safety meetings are held monthly and are based on safety communication best practices. Employees are encouraged to participate in safety audits and report hazards without fear of reprisal.
Outcome: The company maintains a low rate of workplace accidents and high employee satisfaction related to workplace safety. Compliance with safety standards has also enhanced the company’s reputation and productivity.
The Ultimate Guide
to Safety Inspections
Checklists, tools, and best practices to help you meet the safety regulations for your industry
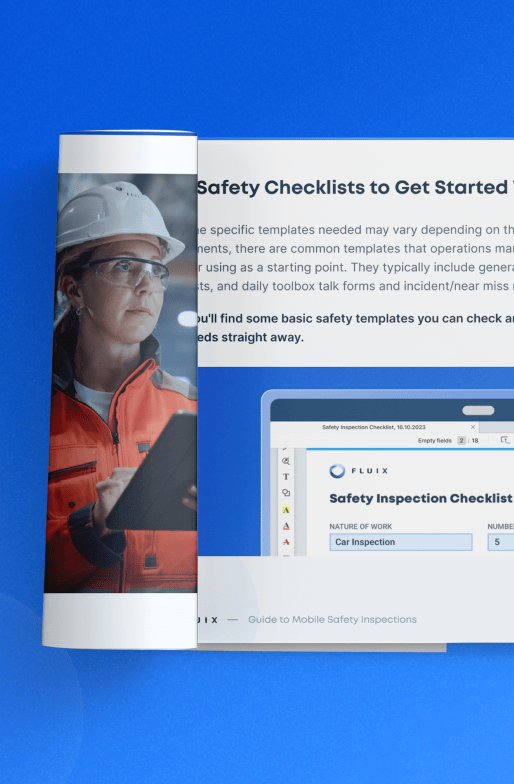
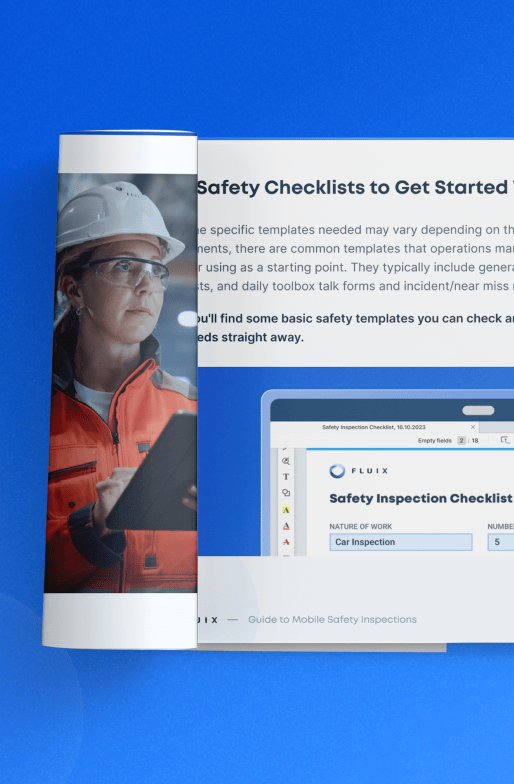
Bad Safety Compliance Example
Scenario: A construction company with frequent changes in work sites and a diverse workforce.
This company practices the following safety compliance lapses:
- Inadequate Training: Employees often start work with minimal training. The training provided is generic and not specific to the particular hazards of current job sites.
- Poor Maintenance: Safety equipment and machinery are poorly maintained; for example, scaffolding is often found to be unstable, and protective gear is worn out or insufficient.
- Lack of Communication: There is no clear channel for reporting safety concerns. Employees often don’t know who to report to. There is a culture of ignoring safety issues to avoid delays in project timelines.
- Insufficient Risk Assessments: Risk assessments are rarely conducted. When they are, they do not cover all potential hazards, and are not communicated effectively to all employees.
- Emergency Unpreparedness: Emergency procedures are outdated, and employees are unfamiliar with evacuation routes or procedures, as drills are infrequent or skipped altogether.
Outcome: There is a high incidence of accidents and injuries, legal penalties, decreased employee morale, and potential long-term legal and financial repercussions for the company.
Can you apply any of the above to your workplace? Act now if you think anything around health and safety compliance and risk management be improved to avoid paying the price later.
How to Ensure Safety Compliance
Ensuring safety compliance is crucial for mitigating risks and protecting your workforce. Here are key strategies to achieve this.
1. Comprehensive Training Programs
Regular training on safety is vital. Each training module you’ll run should address the unique hazards and safety procedures relevant to different roles within your organization or particular jobs.
Incorporating hands-on training sessions, such as simulations and drills, helps reinforce theoretical knowledge with practical experience. And regular refresher courses are necessary to keep all employees up-to-date with the latest safety standards and practices.
Example: A utilities company should provide lineman training on electrical safety, including proper procedures for working on high-voltage lines. This is not only compliant, but could save lives.
2. Applicable Policies
Clear, concise safety policies are fundamental for guiding organizational behavior which in turn helps ensure safety in the work environment.
For them to actually work, the policies should be easily understood and readily accessible to all employees, both in common areas and digitally on the company’s intranet.
One of the ways to achieve this is to involve people in the policy-making process, enhancing their commitment to adhering to safety guidelines. Effective communication of policy updates through multiple channels, such as email, meetings, and newsletters, keeps everyone informed.
Example: A wind turbine plant should implement a safety policy that requires regular inspections and maintenance of utility infrastructure to prevent failures and preempt malfunctions.
3. Regular Audits
Organizations that conduct safety audits on a regular basis would always ensure compliance with regulations more effectively. Both internal and external audits should be scheduled periodically to provide a comprehensive assessment.
One element that ensures a detailed evaluation is a thorough audit checklist covering all aspects of the safety management system, from training records to equipment maintenance. That’s why its design is very important.
Analyzing audit findings is another component of the strategy. It helps identify trends, root causes of non-compliance, and opportunities for improvement, with all steps documented to resolve issues efficiently.
Example: An aviation company conducts internal audits with a team of safety officers, maintenance personnel, and flight operations staff, reviewing operational procedures and maintenance logs.
4. Detailed Protocols
Detailed safety protocols provide specific guidelines for employees to follow in various scenarios, ensuring consistent adherence to safety standards.
Step-by-step instructions for all tasks should emphasize proper procedures and potential hazards, supported by checklists and visual aids to facilitate correct and consistent execution.
And regular walkthroughs and drills help practice these protocols, identifying and addressing any gaps or weaknesses.
Example: A construction company may introduce a ‘safe use of scaffolding’ protocol. To ensure the safe erection, use, and dismantling of scaffolding reducing the risk of falls and other related injuries.
Adopting Effective Ways to Improve Safety Compliance
Once you have ensured effective safety management practices, you need to keep improving it as regulations and workplace realities change.
Fluix is workflow automation software that can help you keep the regulators happy by:
- Improving your safety program by easily sharing manuals, procedures, checklists, tool box talks and documents in the digital format with employees and contractors.
- Ensuring that your protocols are up to date and easily accessible to the people who need them most onsite, offshore and out in the field.
- Keeping auditing paper trails organized, so sharing compliance documentation and reporting safety becomes a digitalized, automated process, eliminating days of paperwork
By leveraging Fluix software, your organization can stay ahead of evolving HSE regulations, helping you build a safer working environment.