Success in any construction project lays on three pillars: budget, time, and quality of the final build. And while the first two elements can be reviewed and adapted, the quality always remains a non-changing component, applying to each stage, from planning and estimation to construction defect inspections.
The better and faster communication between owners, contactors, builders, and inspectors at every step, the more chances of achieving zero defects, reaching a zero building defects list and preventing rework and margin erosions.
Contents:
What Is Zero Defects?
Generally speaking, Zero Defects (you may find it referred to as philosophy of zero defects) in construction is a quality management approach that aims to eliminate errors and defects from the construction process, ensuring that the final product meets the specified quality standards.
This concept is taken from the broader Total Quality Management (TQM) philosophy, which focuses on continuous improvement and customer satisfaction.
An owner, contractor, architect, engineer, designer, construction worker, regulatory officer, insurance provider – if you’re in construction, you need to care about the concept because it has a significant impact on the site safety, quality, and overall performance of your projects.
The Principles of Zero Defects
The principles of zero defects are a set of best practices you can use to achieve excellence in your projects by minimizing/avoiding defects, errors, and rework.
They all to some extent focus on prevention but are not limited to it. Here are the key ones:
- Prevention: Prevention is better than detection and correction of the mistakes after they occur. By addressing planning, design reviews, and risk assessments proactively, you identify potential issues early in the project, and minimize the likelihood of defects occurring.
- Training: Ensuring all your people are adequately trained is fundamental, and training programs you do should cover safety protocols, construction techniques, and quality standards.
- Communication: Architects, engineers, contractors, and subcontractors must effectively collaborate in the construction sites, sharing information and updates to ensure everyone is aligned with the project’s objectives and quality requirements.
- Quality control and assurance: Regular inspections, quality audits, and performance reviews at various project stages help identify deviations from standards and facilitate timely corrections.
- Improvement: As part of continuous improvement, you need to have post-project reviews and feedback to identify areas for enhancement, which can be applied to raise overall quality standards.
- Client engagement: Regular updates, progress reports, and client feedback mechanisms ensure that the final product aligns with the client’s vision and requirements.
- Documentation: Maintaining comprehensive documentation of project activities, including lessons learned, best practices, and historical data, helps prevent the recurrence of past issues.
- Safety: Ensuring a safe working environment not only protects workers but also prevents accidents and defects that can arise from unsafe practices.
Learn how Centuri updates their field teams with safety toolbox talks using Fluix
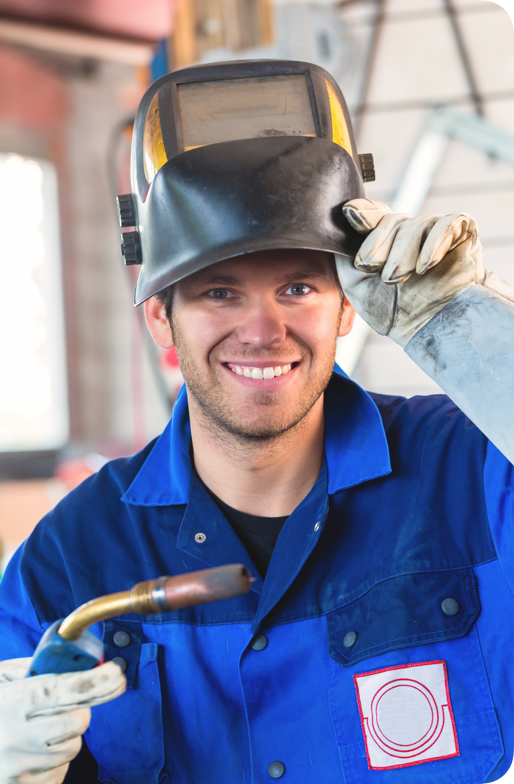
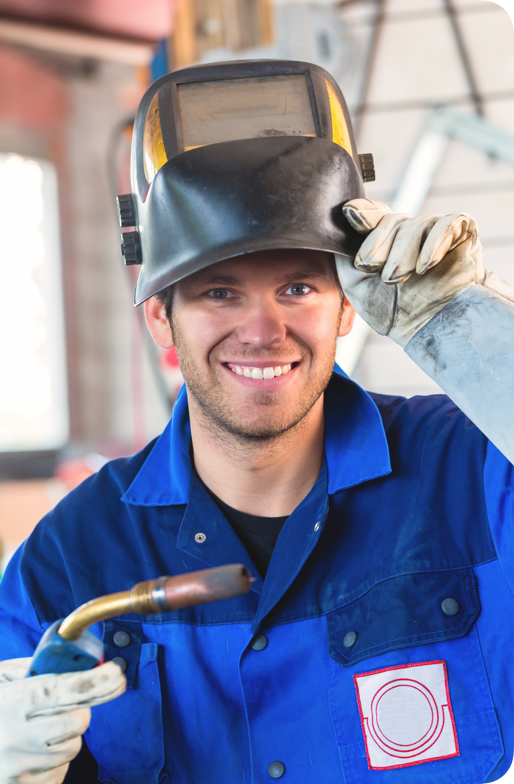
Types of Construction Defects, Causes and Remedies
A construction defect is a deficiency or damage occurring at any stage of the building process, which leads to a failure in its completion, and prevents the structure from being built, or at least causes a significant delay.
Philosophy of zero defects varies, and there are factors affecting the final result besides internal affairs, outsourced logistics or weather conditions, to name a few. However, most typically flaws causing construction delays fall into three categories.
1. No sync between teams
When the jobsite crews, the office, inspectors and stakeholders use different channels for communication, the project slows down. Sometimes, a document can’t make its way through the workflow, waiting for approval by a person unaware of the assignment, and it affects decision making at other stages.
2. Inadequate distribution of documentation
Slow distribution of documents that, despite different automation tools around, are still often sent by mail can cause many issues. Contractors can’t get documents approved and signed on time.
Builders work with older versions of drawings without the latest comments or reviews by the design team. Due to numerous doc variants owners find it hard to track the project progress or detect the responsible for the unfinished tasks.
3. Poor quality control
Poor quality of construction work during production often roots in inadequate quality control procedures. Low-quality substitute materials, lack of time, unskilled laborers, forced due dates, all have a considerable influence on the process and defect quality. Exploring ways to improve construction labour roductivity can mitigate these challenges.
The absence of a proper inspection plan prevents from detecting such flows in early stages, which doubles the cost of remedial works.
How to Improve Your Construction Project Quality
1. Use a cloud-based platform for document management
There are lot of different kinds of documents that go along with any project:
Manage all the docs with one construction field service software, and make sure all the people involved in the project have access to it. Eliminating paper and switching to digital forms will reduce document damage or loss, and speed up distribution between international teams.
Moreover, using dedicated digital platforms helps coordinate, verify and approve the documentation in one place, as all users will have access to the the daily construction report and the latest version with new comments and reviews.
2. Implement proper quality control
It’s essential to introduce quality control for the construction industry. Specify appropriate standards for compliance and product performance at every project stage. It will give a stricter control, and a clearer division of responsibility. Set instant notifications for the emergency cases: this way the task assignees and all the responsible will be immediately reported in case of the accident.
Introduce regular checks for construction defect discovery before final inspections. Keep the records in a digital format, giving the possibility to link up different stages of document edition and modification. Owners, architects and inspectors need to have access to punch lists and inspections lists, easily identifying the elements that require updating.
3. Take care of safety
Research suggests there is a correlation between defects and safety incidents. To avoid it, finalize project design and procurement before construction starts. In the process, deliver regular safety talks, explaining to your crews how to operate safely and with confidence.
Distribute safety protocols and make sure employees understand the requirements in them. Sometimes people may be reluctant to clarify issues because they don’t want to look ignorant or unprofessional. This can lead to incorrectly performed jobsite tasks and eventual defects.
That’s why your teams should easily access the latest safety data sheets, leave comments and consult their creators on whatever questions they may have.
4. Analyze data
Construction workflows are crucial in order to track work for proof of performance and quality control. And for many small construction companies, including remodelers and residential builders, this is all you need, as long as you extract the relevant data from your forms and documents to speed up how change orders turn into invoices and revenue for your company.
However, nearly all larger construction projects require robust project management software, where data from your documents needs to be analyzed and reviewed in as close to real-time as possible.
Last Word
Construction defects can be hard to identify and costly to fix, which can threaten the completion of the whole project. The properly designed communication, organized documentation and quality control process are among the most effective ways to minimize flow occurrence, avoid rework, save your bottom line and protect your reputation.
We at Fluix can help you with this. Fluix is a versatile construction management solution designed to facilitate document management and workflow automation, offering myriad features to help achieve Zero Defects in your construction projects.
By streamlining document control, collaboration, and compliance processes, Fluix can ensure you have consistency in project execution, your documents are always updated, reducing the risk of outdated or erroneous information.
Moreover, Fluix’s task automation and tracking capabilities enhance accountability, preventing critical lapses. With mobile accessibility, teams stay synchronized on-site, mitigating communication gaps and costly errors. If you have any questions, our team will be happy to help and assist with whatever settings you may have.