Quality control and inspection difference
Firstly, let’s define what Quality control and Quality control inspection mean. Quality Control is a process that ensures that the manufactured product, provided service or delivered project adheres to the quality criteria and meets customer requirements. Quality control inspection is an activity intended to monitor and test the ongoing state of works, identify and report non-compliance and verify whether the work is executed inline with the applicable specifications.
To help teams streamline the inspection, its process should be automated.
How to automate the quality control inspection process?
The key figures of quality control inspection are usually made up of two teams: Field team (Site Engineers) working on a particular construction site, and Quality team, who firstly review field team’s findings (Quality Managers) and then approve taken findings by responsible parties (Project Managers and Head Engineer).
Let’s map the flowchart for the mentioned groups:
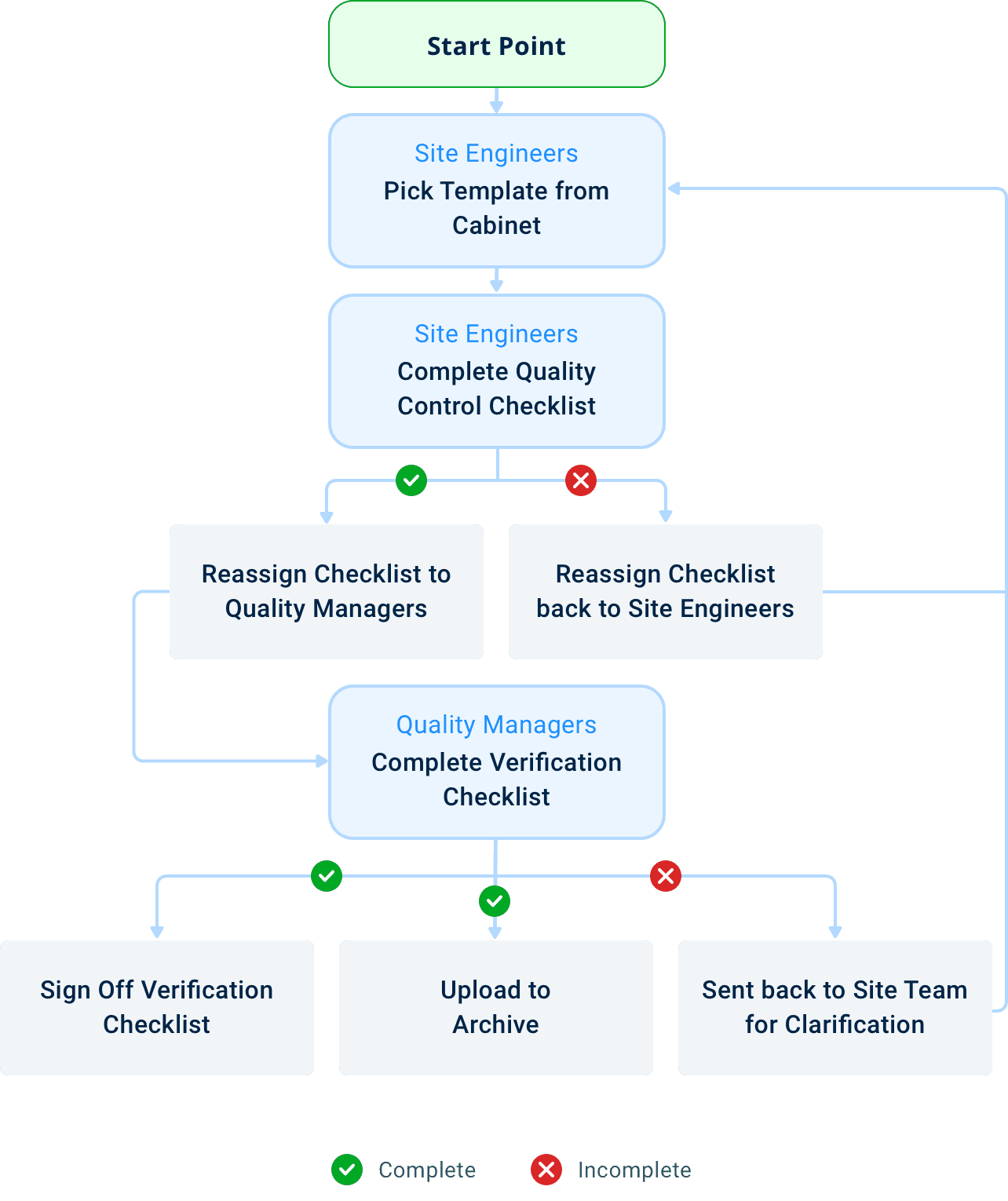
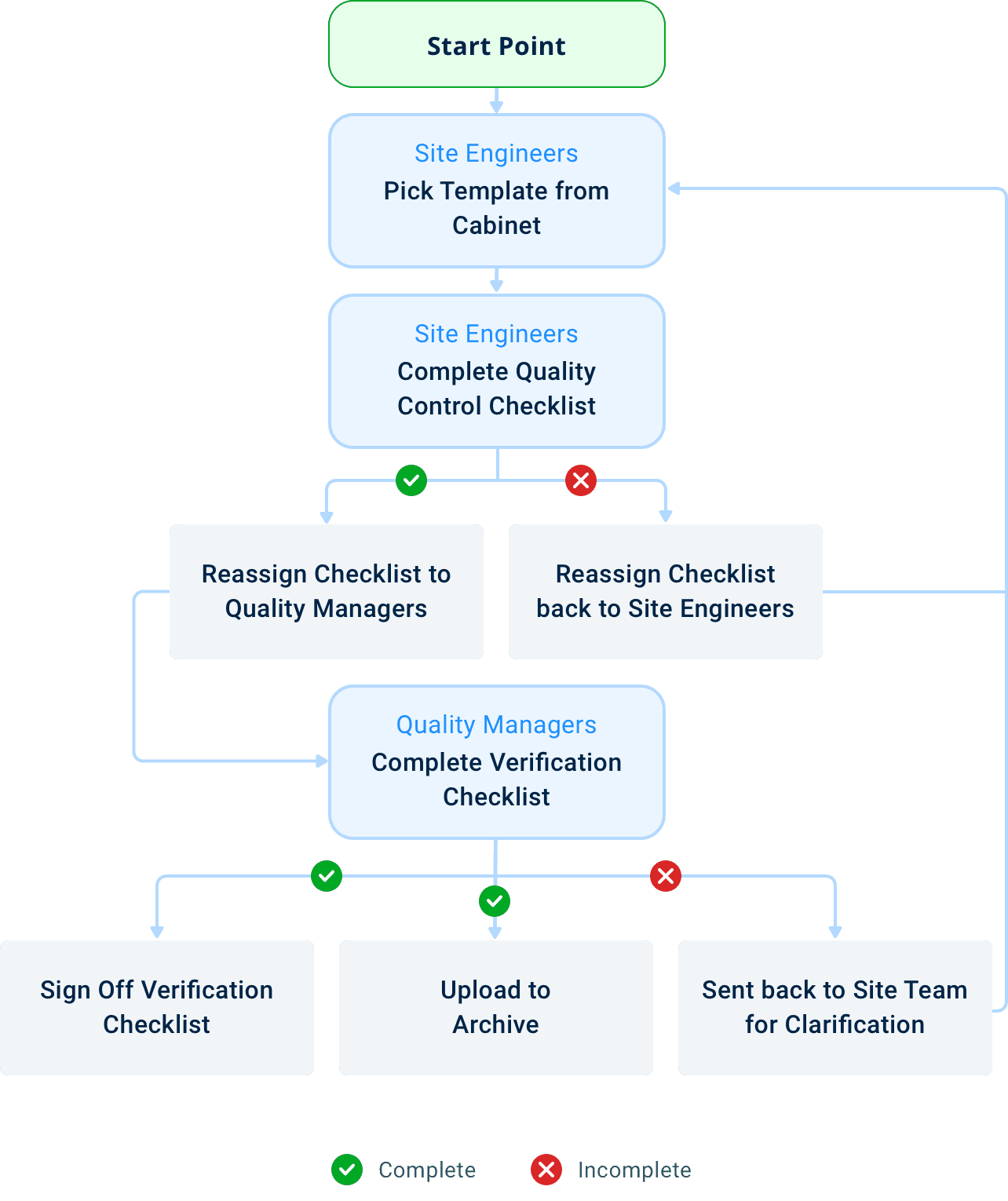
Check how to build your process in Fluix
Here are the steps:
There are four main steps that allow these two groups to ensure the quality of work performed at every step of the project.
- Site Engineers: Add details
- Site Engineers: Complete Quality Control Checklist
- Quality Team: Complete Verification Checklist
- Quality Team: Sign off Verification Checklist
Depending on your organization’s structure, some responsibilities in the onboarding process may be shared by various personnel. The contributors are responsible for creating the onboarding checklist template. Senior management or HR can be tasked with making sure that each part of the process is properly assigned and completed.
Quality control inspection software in action
Quality control inspection software has to meet the requirements of both field teams and office crew. Here are the main ones.
- Collaborating on QC inspection checklists
The start point of inspection paperwork is collecting raw data. Fluix mobile app allows Site engineers to fill out quality control inspection forms, add measurements, comments, photos with timestamps and geolocation, and finally sign the completed form. All that is possible on an iPad or iPhone, even without connectivity.Since multiple people may work on the same quality control inspection checklist for a longer time, it is usually important for them to have access to the same document in progress. In Fluix app team members get a shared work environment where they can collaborate on the same forms and assign them to each other. In this way working in shifts is no longer a problem since the checklist can be assigned to the team member if it’s not completed before the shift is over.Finally, Fluix mobile app allows engineers to jump between the documents under different inspections and projects, within one account, making paperwork even easier. - Slashing the review process time
The very moment a Site engineer completes the quality control inspection checklist, it is reassigned to the Quality team for review. If the checklist requires rework, the Quality manager can easily return it back to the Site engineers, with comments on what should be corrected. Once all remarks are fixed, Site engineer sends the checklist for another review. The whole review and approval cycle can be also done on mobile devices, right on site. The configured approval workflow allows teams to exchange checklists and comments in an efficient way, without clarification emails and calls. - Perks for Project Leads
One of the most annoying things for the Project lead is to waste time on administration work. This is why it’s crucial to choose a quality control inspection program that offers extensive capabilities and doesn’t require time for their support. Here are some:- Easily add new engineers to work on a project by adding them to right groups
- Remove engineers from groups who no longer work on the project and reassign documents in progress to the right engineer
- Track progress on the checklists in progress from Document Status section on the backend
- Provide granular permissions to those engineers who need extra access or visibility to documents in progress, data storage and reporting
- Set naming convention to the templates of quality control checklists to have all the documents named according to the same pattern automatically, which makes it fast to locate them
- Store or act on data?
When the review is done, the signed quality control checklist usually flies to the office email and archive folder for safekeeping. Fluix offers both its internal cloud storage or integration with familiar storage such as Google Drive, Dropbox, OneDrive, Box and others.Along with archiving of the completed files Fluix offers to look at data as insights. Data reporting and analysis capabilities allow you to prepare filtered reports and export them in Excel, or third party visualization platforms for further sharing with site teams, managers and customers.
To cover the key aspects of the process, we recommend using these checklists:
Advice from practice
Quality control inspection is an integral part of any construction project, manufacturing, and other spheres where quality is crucial for people safety, high quality of performed work, and consequently reduced costs on maintenance and repairs of the produced or built asset. That is why it’s absolutely crucial to choose the right system that will automate the whole process, no matter how complex it is, the system that is flexible and scalable, the tool that is stable and easy to use.