A personal protective equipment (PPE) checklist is a document that ensures all equipment is readily available, working properly, and suited for the job.
In industries like construction, energy, and manufacturing, using a PPE checklist can help create a safe work environment while empowering your teams to work efficiently every day.
Typically, a site supervisor, safety manager, or designated team lead is responsible for completing and managing these PPE checklists.
However, depending on the team size and safety inspection process requirements, individual team members may also be assigned to inspect their own equipment before starting each shift.
What Should Be Included in a PPE Checklist?
A comprehensive PPE checklist is designed to fit the specific needs of your work environment, covering everything from head protection to respiratory gear. So, what are the essentials?
- General PPE Requirements. This section should cover inspection schedules, guidelines for replacing worn or expired equipment, and basic maintenance steps to keep PPE in top condition.
- Head Protection. The types of head protection required, along with maintenance reminders to keep them clean and damage-free.
- Eye and Face Protection. For environments with safety hazards and risks to the eyes and face, such as flying particles or chemical splashes, eye and face protection like goggles and face shields are a must.
- Hearing Protection. If noise levels exceed safe thresholds, earmuffs and earplugs are essential to prevent hearing damage. This section should ensure hearing protection is available and inspected regularly, with noise hazard areas clearly marked.
- Hand Protection. Gloves safeguard hands from cuts, chemicals, extreme temperatures, and other hazards. Your checklist should specify the right glove types for each task and verify that they’re undamaged and properly fitted.
- Foot Protection. The right footwear protects against various risks, from slips and chemical spills to electrical hazards. Ensure the checklist covers maintenance for protective footwear and includes requirements specific to the site.
- Respiratory Protection. Respirators and masks protect against dust, fumes, and airborne contaminants. This section should confirm that respirators are clean, fitted, and properly maintained, with reminders to check filters for wear.
- Full-Body Protection. For tasks involving hazardous materials or extreme conditions, full-body suits or coveralls are essential. Your checklist should ensure that protective clothing is free of contaminants and stored properly, with a focus on training employees on proper use.
By covering this essential gear and maintenance, you’re fostering a proactive safety culture that keeps your team prepared and protected.
The Ultimate Guide
to Safety Inspections
Checklists, tools, and best practices to help you meet the safety regulations for your industry and don’t risk fines
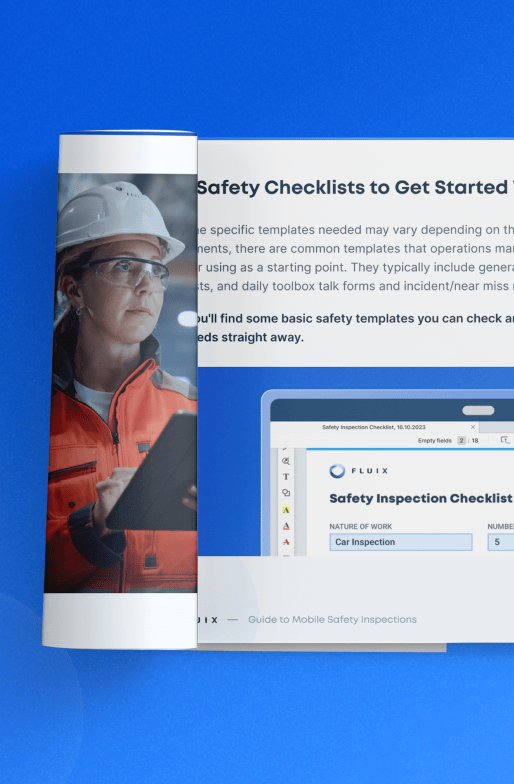
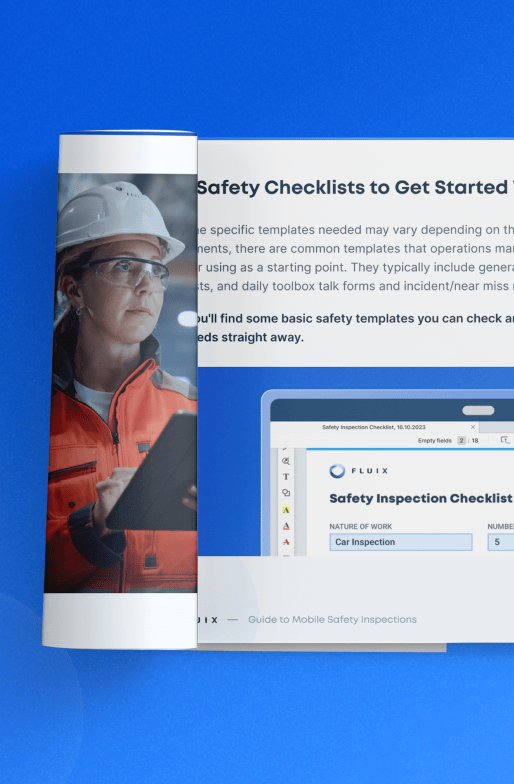
Why It’s More Effective to Use a Digital PPE Inspection Checklist
Why bother with a paper checklist when a digital one can make life easier for you and your team?
Transitioning to a digital PPE checklist streamlines everything, including compliance with safety regulations, offering some game-changing advantages that reduce errors. Here’s what you stand to gain:
- Improved Safety. Track inspections thoroughly and quickly, reducing the chance of overlooking damaged PPE.
- Improved Compliance. Comply with OSHA standards and document safety protocols, so you’re always audit-ready and confident that you’re building a safety culture.
- Faster Fixes. When inspection reports are automated, you’re able to address issues instantly. Defects don’t linger, and you don’t have to rely on memory or manual tracking – your digital checklist sends alerts so you can keep everyone safe without delay.
- Enhanced Accuracy. With digital input, you eliminate the risk of handwriting errors or misplaced paperwork.
- Time Savings. By digitizing checklists, field teams can speed up reporting and streamline data entry, freeing up more time to focus on high-priority tasks.
Switching to digital PPE checklists isn’t just about convenience; it’s about empowering your team with tools that improve safety, efficiency, and peace of mind.
How You Can Manage Your PPE Checklists Templates with Fluix
Fluix is field productivity software that offers everything you need to streamline your PPE checklists with ease and efficiency. Here’s how:
- PDF and Web Form Support. Fluix supports both fillable PDFs and dynamic forms, giving you the flexibility to build and customize checklists that fit your specific needs.
- Access on Any Device. With Fluix’s mobile app, your team can access PPE checklists on iPads, Android tablets, or in a web browser. This multi-device support ensures that everyone has access, no matter where they are in the field.
- Work Offline, Sync When Online. Fluix’s offline data collection keeps your field teams productive, even in remote locations. They can complete checklists offline and sync the data automatically when back online, eliminating delays and data loss.
- Form Builder and Template Library. The form builder allows you to create or modify PPE checklist templates with ease. Choose from a library of ready-to-use templates or customize your own.
- Automated Inspection Workflows. Set up automated workflows to route completed checklists to the appropriate team members, trigger notifications for urgent issues, and manage approvals – all in one system.
With Fluix, managing your PPE checklist templates becomes a seamless, organized, and highly efficient process that saves time, boosts accountability, and keeps safety at the forefront.