A machine guarding checklist (machine safety checklist) is a document that organizes essential safety checks and maintenance tasks for machines, focusing on guards and safety barriers to protect workers from injuries due to moving parts, nonmechanical and mechanical hazards, and flying debris.
Every machine in a facility has unique hazards and the machine guard acts as the first line of defense. It can prevent injuries like broken fingers, burns, and other common accidents.
In regulated industries, the stakes are high: without these safeguards, companies risk costly fines or citations if inspectors identify safety issues.
What’s Included in a Machine Guarding Checklist?
A comprehensive checklist covers multiple areas of machinery safety, ensuring nothing is missed. Here are the seven main components to include:
1. General Safeguard Assessment
This section examines the overall condition and functionality of the machine’s safeguard. Key areas covered include:
- Security of safeguards
- Contact prevention
- Protection from falling objects
- Comfort and safety
2. Point of Operation Safety
This component focuses on the specific area where the machine interacts with material or the operator performs a function:
- Presence of guard
- Operator safety
- Tampering and removal
3. Mechanical Hazard Assessment
This component deals with identifying and addressing mechanical hazards that may exist on or around the machinery:
- Unprotected moving parts
- Starting and stopping controls
- Multi-Operator Access
4. Nonmechanical Hazard Assessment
Nonmechanical hazards, such as noise require the following checks:
- Noise hazards
- PPE for nonmechanical risks
- Environmental safeguards
5. Electrical Hazard Safeguards
This component focuses on potential electrical hazards associated with the machinery:
- Proper grounding
- Fused and guarded power supply
- Loose fittings and minor shocks
6. Maintenance and Repair Protocols
This section ensures safety protocols during repair and maintenance are followed:
- Lockout/tagout compliance
- Multiple lockout devices
- Use of PPE
7. Employee Training
This section ensures that workers completed safety training and aware of the safety measures in place:
- Operator training
- Up-to-date maintenance training
- Incident response training
By covering these s components, a machine guarding checklist ensures that all potential risks are managed, promoting a safe working environment.
The Ultimate Guide
to Safety Inspections
Checklists, tools, and best practices to help you meet the safety regulations for your industry and don’t risk fines
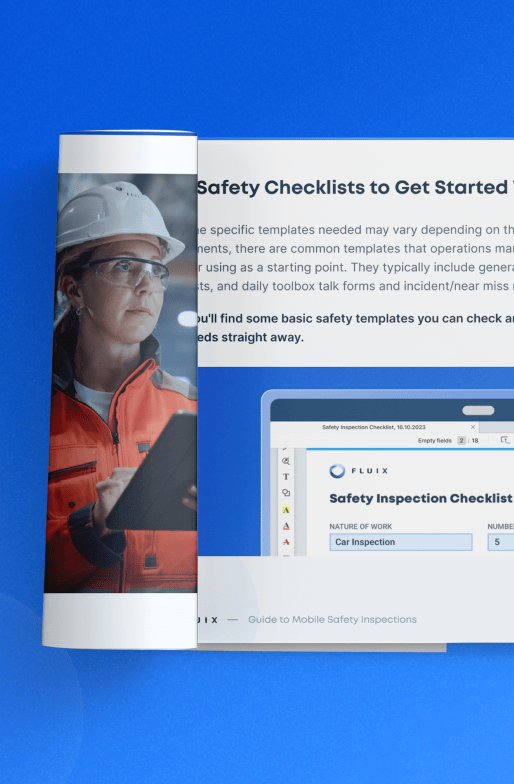
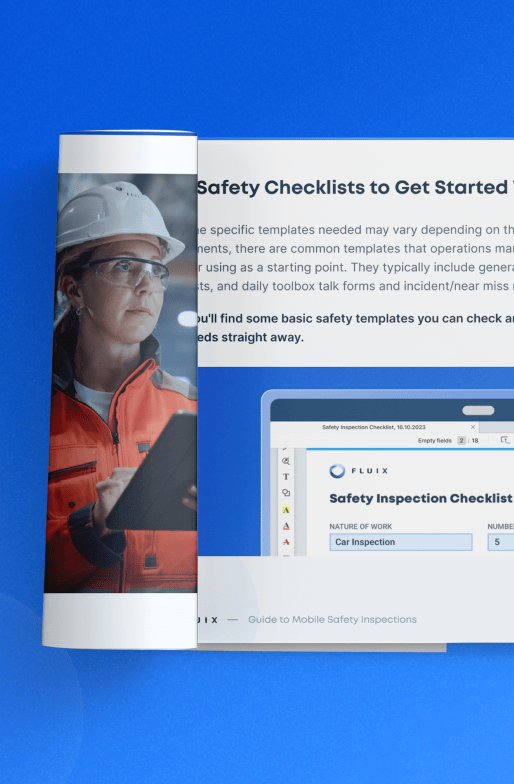
Why It’s More Effective to Use Digital Machine Guarding Checklists
Switching from paper to digital checklists offers substantial benefits, enhancing both safety and efficiency. Here’s why it makes a difference:
- Routine, Complete Inspections: Digital checklists help prevent “visual-only” inspections by ensuring that each check is fully documented and trackable.
- Faster Maintenance and Repairs: With automation, you’ll know exactly when a machine needs repair, which reduces downtime and minimizes risk.
- Regulatory Compliance and Peace of Mind: Digital tracking gives you proof of compliance, showing that you’re following all machine safety regulations.
- Longer Machinery Lifespan: Routine maintenance and repairs help extend the life of your machines, saving you costs on replacements.
How Fluix Can Help You Manage Machine Guarding Checklist
Fluix is field productivity software that offers all the tools you need to digitize your machine guarding and make it straightforward and efficient.
- Customizable Form Builder. Build any checklist using Fluix’s drag-and-drop form builder. This tool allows you to add fields, instructions, and requirements to ensure your checklist covers every critical point.
- Digital Checklists and Template Library. You can keep all your templates – fillable PDFs or web forms – organized and ready for use, so your admins can pull up consistent, compliant checklists instantly and use them across different machines and inspections.
- Comments for Detailed Documentation. Fluix’s comments and forms feature lets inspectors add notes or attach relevant documents if they spot an issue, making it easy to capture and communicate critical information on the spot.
- Task Assignments. If an inspection identifies issues that require immediate action, Fluix’s task assignment feature allows you to assign these follow-up tasks right within the app.
- Automated Approvals. Fluix integrates approval steps directly into your workflow, allowing managers or safety officers to review and sign off on completed inspections.
By using these features, your team gets an efficient way to handle machine guarding, from checklist creation to final approvals. No more lost paperwork, missed steps, or miscommunications – just a fully digital process that saves time, boosts field productivity, and keeps your site safe.