Imagine starting each workday with a burst of energy and focus on safety. Toolbox talks can do just that, turning routine meetings into powerful moments of connection and learning.
Whether you’re new to running these talks or looking to enhance their effectiveness, this article will provide you with the insights and tips you need. We’ll explore the role of toolbox talks in safety, and dive into the details for planning and execution.
Contents:
What Is a Toolbox Talk?
A toolbox talk is a short and informal safety meeting between supervisors or managers and their teams.
Held before the start of a shift or workday, each session focuses on a specific safety topic. These quick and casual chats are designed to be straightforward and easy for everyone to understand. They are a simple way to help build a safety culture within your organization.
Depending on the industry and region, they may be called:
- safety talks
- safety chats
- safety time-outs
- safety minutes
- safety moments
- safety briefings
- take 5 safety talks
- pre-start talks
- tailgate talks
- tailgate meetings
- toolbox meetings
No matter the name, the outcome will be the same if executed properly: a safer work environment.
Read More Read More How RWE is distributing safety talk documents more efficiently than ever before
The Purpose of a Toolbox Talk
The main goal of a toolbox talk is to keep safety topics fresh and top-of-mind for team members.
These sessions are meant to supplement mandatory safety training. Toolbox meetings do this by reiterating key safety practices and procedures, educating employees about potential hazards, and emphasizing the importance of staying safe.
Since formal training sessions aren’t held often, these talks provide frequent opportunities to reinforce knowledge and promote safety awareness across the team.
Toolbox meetings are an essential part of a safety management system (SMS). They serve as practical, on-the-ground reminders of principles and protocols outlined in the SMS.
Toolbox Talk Details: Key Roles, Duration, Frequency, and Regulations
To make the most of your safety talks, it’s important to grasp the operational elements involved. Here’s what you need to know:
Who should run a toolbox meeting?
Toolbox talks are usually led by a supervisor, manager, forman, or safety officer. These individuals are often closest to the day-to-day operations and are well-positioned to identify relevant safety topics and address any immediate concerns.
However, safety briefings can be run by anyone with the right knowledge and experience, whether it’s a crew lead, a safety consultant, or the company director.
Safety management software can help organize and assign toolbox talk responsibilities efficiently.
How long is a toolbox talk?
A well-run talk should last between 5 to 15 minutes. That’s enough time to cover important safety points without disrupting the workday too much. By maintaining this balance, you can significantly improve safety in the workplace.
Please note that the length can vary depending on the topic and the team’s needs.
How often should toolbox talks be conducted?
Most companies hold safety chats daily. Some choose to hold them weekly or monthly, depending on what works best for their operations.
Keep in mind that regularity helps ensure safety compliance.
Are there any toolbox talk regulations?
Unlike mandatory training sessions and formal safety meetings, toolbox talks aren’t bound by strict regulations. This flexibility allows them to be tailored to the specific needs and dynamics of your workplace.
The Ultimate Guide
to Safety Inspections
Checklists, tools, and best practices to help you meet the safety regulations for your industry. and don’t risk fines
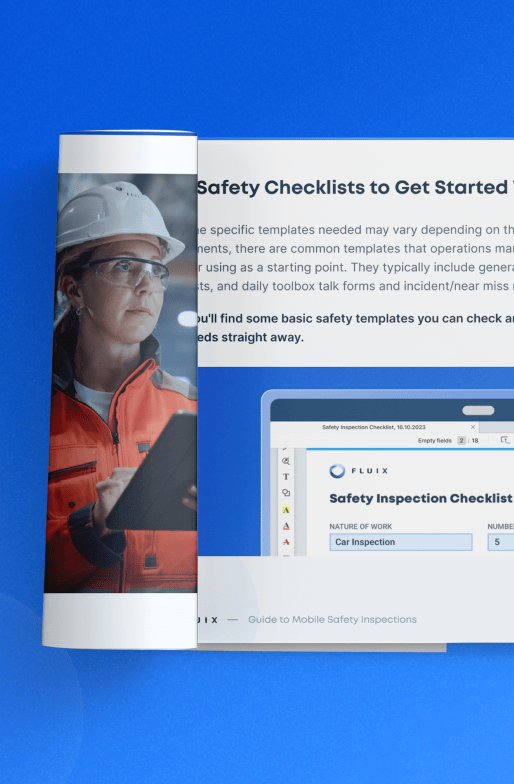
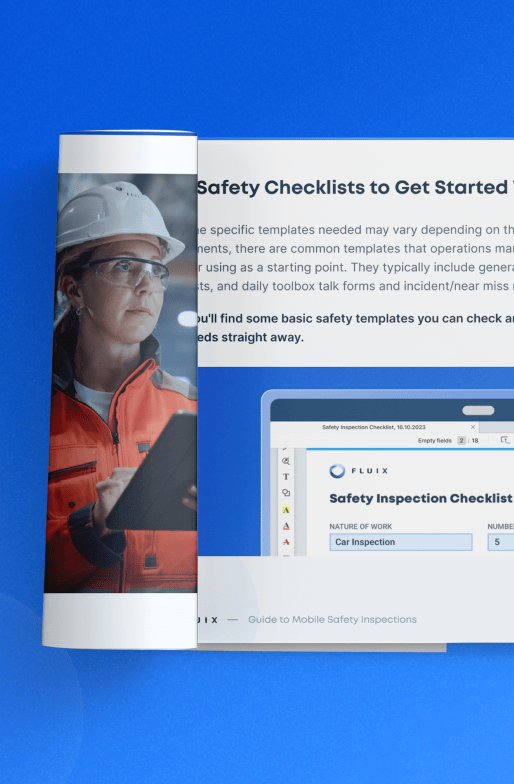
How to Run an Effective Toolbox Meeting
To make your toolbox meetings really count, focus on strategies that keep team members engaged and the discussions on point. Here are some tips to help you achieve that:
1. Pick a relevant topic:
Choose a topic that relates to the day’s tasks or the current work environment. For example, there’s no point in talking about frozen surfaces in the middle of summer. Instead, focus on topics that are timely and pertinent, such as heat exhaustion or sun protection in the summer.
Always aim to address the specific challenges and conditions your team is facing. For inspiration, check out our article on toolbox talk topic ideas.
2. Address worksite changes
Revisit any recent changes to the site or working conditions as a topic in your safety briefings. A refresher before the workday begins can be very effective in reinforcing new protocols.
For instance, if a new piece of heavy machinery has been introduced to the site, it’s beneficial to address safety hazards that might arise from these changes.
Keeping these updates top of mind helps avoid accidents and ensures everyone knows how to navigate the new environment or equipment safely.
3. Keep it simple
There’s no good throwing around a bunch of jargon because it sounds more official. If a team has a common turn of phrase or name for a specific piece of equipment, it’s better to use that than its real name like the FCX5-800; which might not even be recognized.
If people can’t understand what you’re talking about, it’s hard to keep the work environment safe.
4. Make it visual
People remember information better when they can see it in action. To make your safety talks more engaging, try using props or visual aids.
For instance, if you’re discussing the proper fit for safety harnesses, bring one along to demonstrate the fitting process.
Visual elements can make your talks more interactive and memorable.
5. Speak freely
If you know the topic well, look at your team when presenting, rather than reading from notes or a PowerPoint.
This approach shows that you’re knowledgeable and confident about the subject, which helps build trust and encourages more open discussion. It can also improve team communication by making the session more interactive and responsive.
This mode of safety communication is informal, and the way it’s presented should reflect that.
6. Track your talks
It’s a good idea to log all the toolbox talks you conduct at work. Jot down the topic, who led the talk, the date, and whether there were any follow up questions.
Although this isn’t required by OSHA, having this information can be helpful. It lets you see what topics you’ve covered, how long it’s been since you last talked about them, and whether you need to follow up on any questions or concerns raised.
To make it easier, you can record toolbox talks to a template like this one.
Delivering Impactful Toolbox Talks with Fluix
Fluix is safety management software that can assist in facilitating toolbox meetings. We provide a digital platform that streamlines the preparation, delivery, and documentation of these important safety meetings. Here’s how:
- Preparation: Easily organize and access all the documents and templates you need to develop content for your safety chats.
- Delivery: Conduct toolbox talks through our digital platform, enabling team members to access them from remote locations or even when offline.
- Engagement: Track the digital attendance for your safety talks and follow up with quizzes.
- Documentation: Automatically store all the details from your safety briefings, making it easy to follow up on any questions or issues that come up during sessions.
Fluix enhances the organization and administration of safety management, providing a smoother experience for team members and managers alike.