What Is the Work Order Process?
A work order process is a step-by-step system for handling requests, from the moment they’re submitted until the tasks are completed and documented.
You can think of the work order process like a roadmap. Each step marks a key action along the way. These steps include:
- submitting requests
- prioritizing or approving tasks
- assigning technicians
- gathering materials
- carrying out the work
- performing quality checks
- closing the order
When structured well, the work order management process encourages communication, improves visibility, and keeps tasks on track.
Why Is It Important to Have a Work Order Process?
A structured work order process helps you sidestep inefficiencies, miscommunications, and delays. Here’s how it supports smoother operations:
- Efficiency: With clear steps and structure, your team spends less time defining roles, searching for information, and chasing approvals. They can focus on their core tasks, boosting overall productivity.
- Prioritization: An organized system lets you categorize and rank tasks by urgency and impact. Critical issues get fast attention, while routine tasks fit into the schedule without derailing key operations.
- Accountability: Defined roles at each step reduces the risk of tasks slipping through the cracks. Tracking each action also improves accountability for both managers and technicians.
Steps in the Work Order Process
An effective work order procedure takes maintenance requests from messy to manageable. It usually involves four main steps:
1. Formal Work Request
Companies typically have a standard way to report issues or make requests. This might involve submitting a work order form through an online portal or even just by email, for example.
Each request should provide information about the work needed and other relevant details like location and equipment ID.
2. Review and Approval
Depending on the request, a supervisor may need to review and approve it. Larger or higher-cost projects may require extra planning or a closer look from specialists for instance. Companies should specify who can approve each type of request to keep the process smooth.
3. Scheduling and Planning
Requests aren’t always completed in the order they arrive in. Work orders should be prioritized by urgency and matched with technicians who have the right skills and certifications. It’s also important to check if parts are available before scheduling.
4. Assignment and Final Review
Supervisors assign tasks to the relevant technicians. Once the technician completes the job, the supervisor should review the paperwork and close the order if it meets standards.
Transform Your Work Order Process with Fluix: Start Automating Today
Work Order Process Flowchart
Every company will likely have its unique work order process flow. Still, most share several steps and procedures. Here’s a breakdown of a typical workflow.
- Formal Work Request and Approval: An employee makes a formal request using specified channels or forms.
- Approval or Rejection: If the request needs approval, it goes to the appropriate person for review. Approved requests move to scheduling; if more information is needed, the request is sent back to the requester.
- Scheduling and Planning: At this stage, the supervisor assesses what the task requires: specific technicians, parts, tools, documents, etc. This also involves checking inventories and technician availability.
- Assignment and Execution: The supervisor assigns the work order to a technician, providing details and a deadline. The technician completes the task, marks it as done, and sends documentation of the finished work order back to their supervisor.
- Final Review: The supervisor reviews the completed work order to ensure it meets all standards. If everything is in order, they mark it as complete and close the request. If anything needs fixing, they send it back to the technician for a closer look.
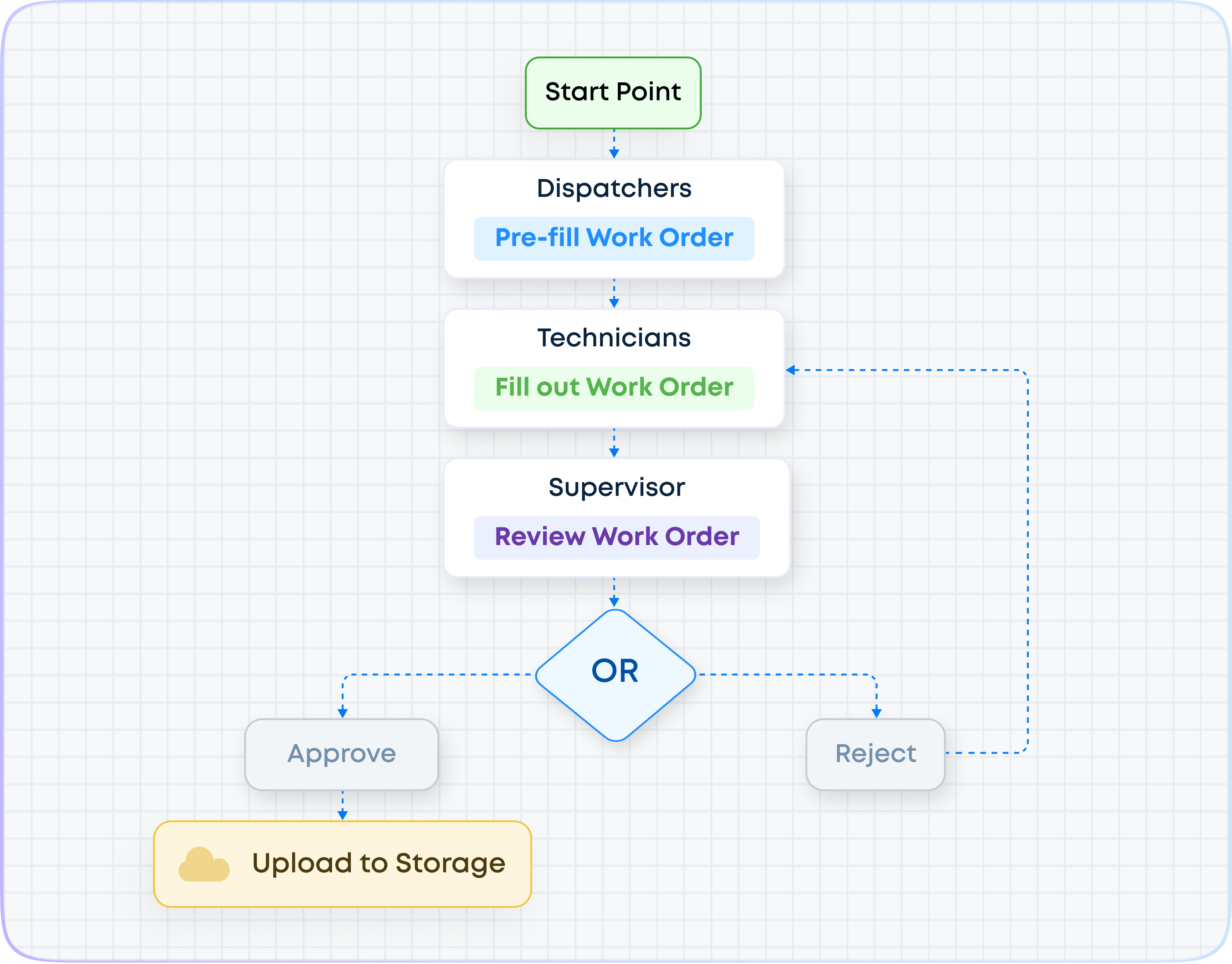
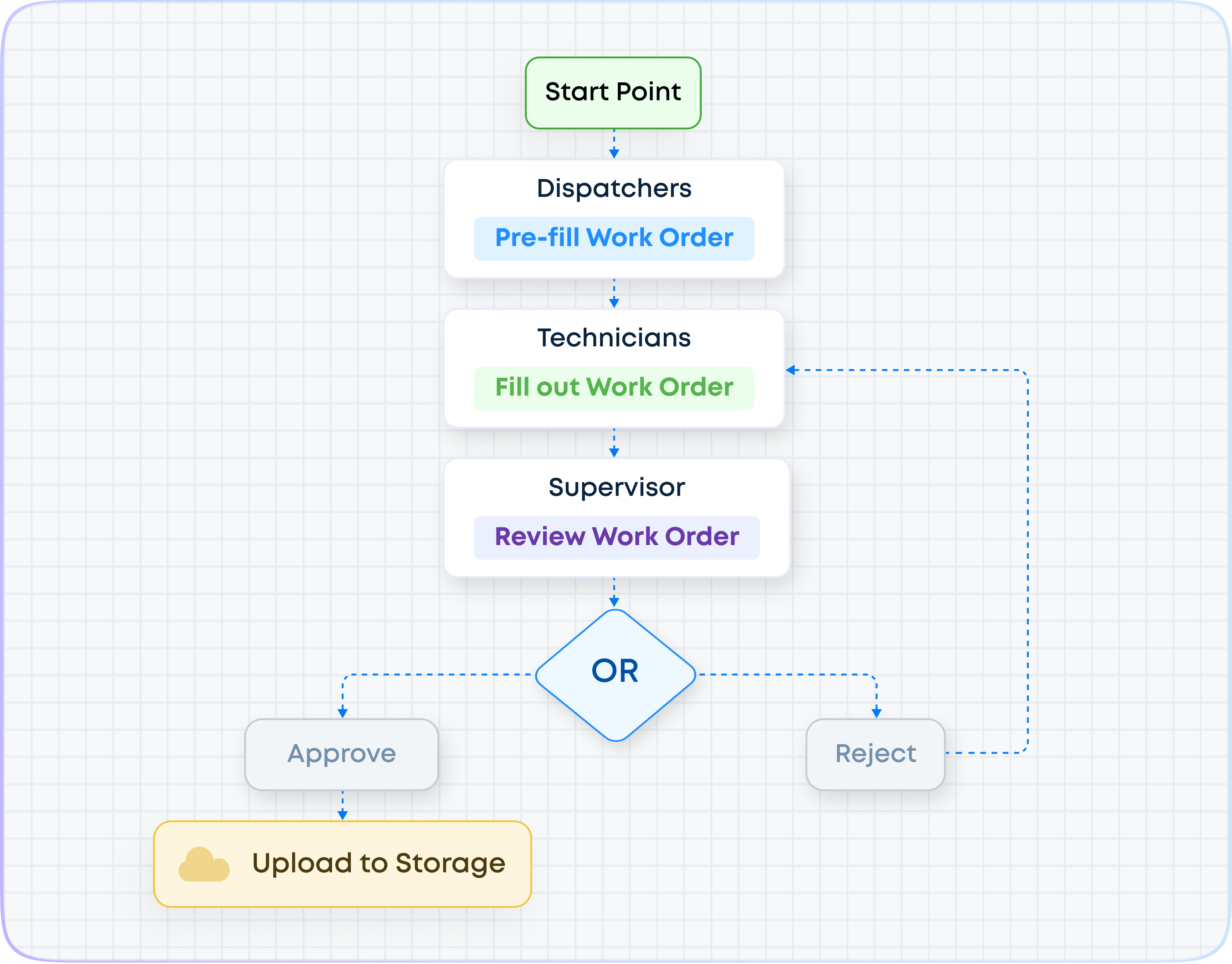
This example provides a general structure, though your company’s approach may require more customization. The work order management process is flexible and should adapt to fit your organization’s needs over time.
To cover the key aspects of the process, we recommend using these checklists:
Challenges of Work Order Processes
You can run into all kinds of issues with your work order procedure, like:
- Miscommunication across teams. If the steps of your process aren’t clear or standardized, information can easily get lost or misinterpreted as it moves from one person to another. Miscommunications can result in delays and mistakes.
- Manual entry errors. Processing work orders manually comes with a high risk of errors—like typos, missing details, or misplaced records. These small mistakes can add up over time, stalling progress and affecting customer satisfaction.
- Tracking delays. If you don’t have a central system to monitor work orders, it’s easy for updates to slip through the cracks. Inconsistent updates make it hard for teams to stay on track, slowing response times and leaving customers unsatisfied.
- Approval bottlenecks. When approvals aren’t streamlined, work orders can get stuck. Bottlenecks from multiple sign-offs, unclear priorities, or inefficient workflows can leave orders waiting in limbo.
- Difficulty in managing high volumes. As the number of work orders grow, using manual or outdated systems quickly becomes overwhelming. You need the right tools to keep up with high demand and avoid costly mistakes.
How to Optimize the Work Order Process
To optimize your work order process, start by talking to the people who use it every day. Gather feedback to learn what’s working, what’s causing slowdowns, and where frustrations arise. This information will help you see both strengths and opportunities for improvement.
Next, you’ll want to consider the ROI of automation. Automating your work order process allows tasks to move seamlessly from one step to the next, without the need for constant oversight.
Equipping your team with mobile documentation tools is also a big efficiency booster. With the ability to submit work orders and review protocols on the go, your team has everything they need to stay productive on-site.
As a final step, make it a habit to review work order metrics consistently. This data-driven approach will help you spot patterns and issues which may have been missed otherwise.
Managing Work Orders with Fluix
Fluix is inspection software that optimizes every step of your work order process. With Fluix, technicians use smart forms that display only the fields they need, capturing essential details quickly and accurately—no wasted time on irrelevant fields.
Your technicians can access relevant documentation on the spot and submit their work orders from anywhere: keeping them productive no matter where they are.
As data is logged, automated workflows instantly route work orders through the right channels, prioritizing them by urgency, complexity, or priority level. Approval cycles are faster and more transparent, and tracking each step of the process is simple.
And by capturing data at each stage, Fluix’s reporting tool lets you monitor key metrics like time-to-complete and resource usage. This data will help you make ongoing improvements to your work order management process.
Fluix brings together all the tools you need to streamline work order management and keep your technicians productive at every job.