Workplace safety is a paramount concern for employers and regulators, particularly when addressing severe work-related injuries.
As safety management software dedicated to helping ensure workplace safety, Fluix has analyzed a rich dataset comprising 85,632 severe injury cases reported under federal OSHA jurisdiction from January 2015 to June 2024.
In the article below, we present the key findings of this analysis, alongside insights into the nature of workplace accidents, their frequency, and the industries most affected.
This data provides insights for safety professionals, offering a fresh perspective on safety protocols and strategies aimed at fostering safer workplaces for all.
Contents:
Key Findings
The present research uses data collected by the Occupational Safety and Health Administration (OSHA). Since January 1, 2015, OSHA has mandated that all employers (USA-based comapnies) report severe incidents, including amputations and in-patient hospitalizations. This requirement serves a crucial role in mitigating workplace hazards and creating a safe work environment.
To date, over 85,000 cases have been reported, and our analysis has revealed key findings essential for understanding workplace safety. We also provide a visual chart for each trend for enhanced comprehension.
Trend Over Time
From 2015 to 2019, there were no sharp fluctuations, but the volume of injuries steadily increased. A particularly significant observation is the impact of the COVID-19 pandemic, as evidenced by a notable drop in severe injuries reported in 2019.
This decline correlates with the implementation of pandemic-related safety measures and restrictions in workplaces across the country.
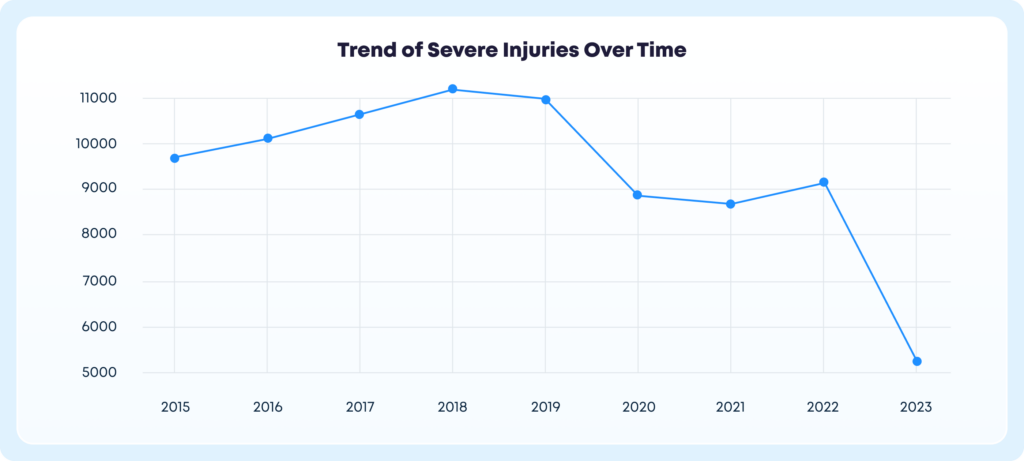
Geographic Distribution
You can see distinct geographic patterns in the distribution of workplace accidents. The heatmap below highlights states such as Texas, Florida, Illinois, Ohio, and Pennsylvania as regions with a higher prevalence of severe injuries.
It’s important to note that this data reflects incidents under federal OSHA jurisdiction and may not capture all workplace accidents due to variations in state reporting requirements.
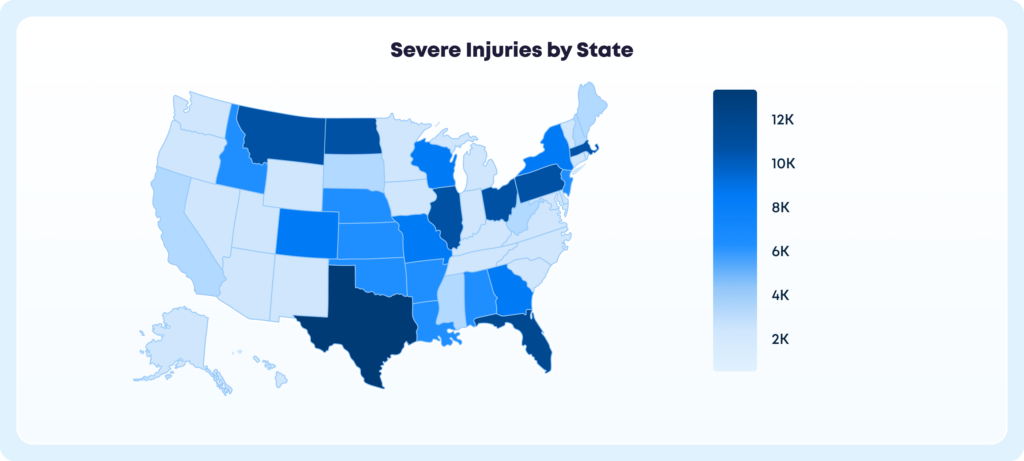
Industry Distribution
Based on the analysis of the distribution of severe injury cases across different industries, surprisingly, the medical industry emerged as the leading sector in terms of reported severe injuries. This indicates potential areas for improvement in workplace safety protocols within healthcare settings.
Correlating injury rates with the total number of businesses employed in each industry can provide a better understanding of safety performance relative to workforce size.
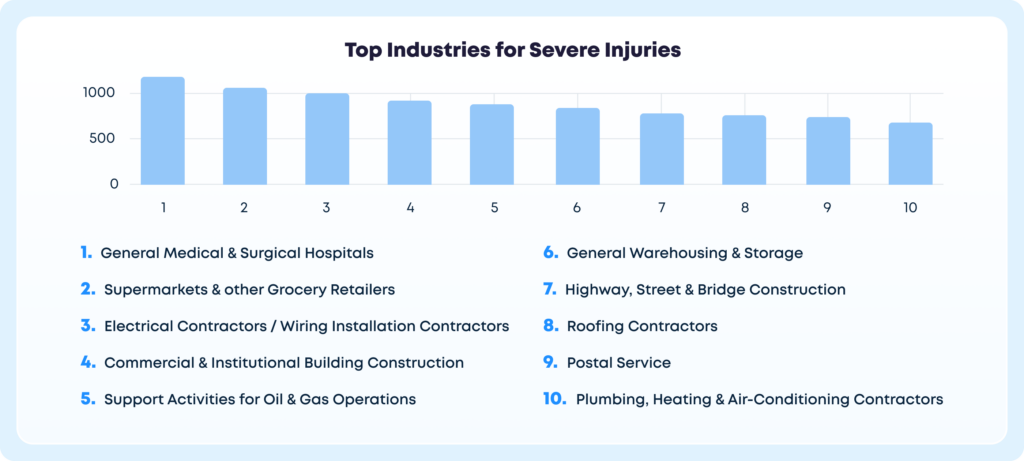
Leading Causes of Severe Injuries
Among the top ten causes identified are falls and machinery-related injuries, underscoring the critical importance of implementing robust safety measures in these areas.
By prioritizing preventive measures targeting these high-risk activities, organizations can effectively mitigate the occurrence of severe injuries and enhance workplace safety for all employees.
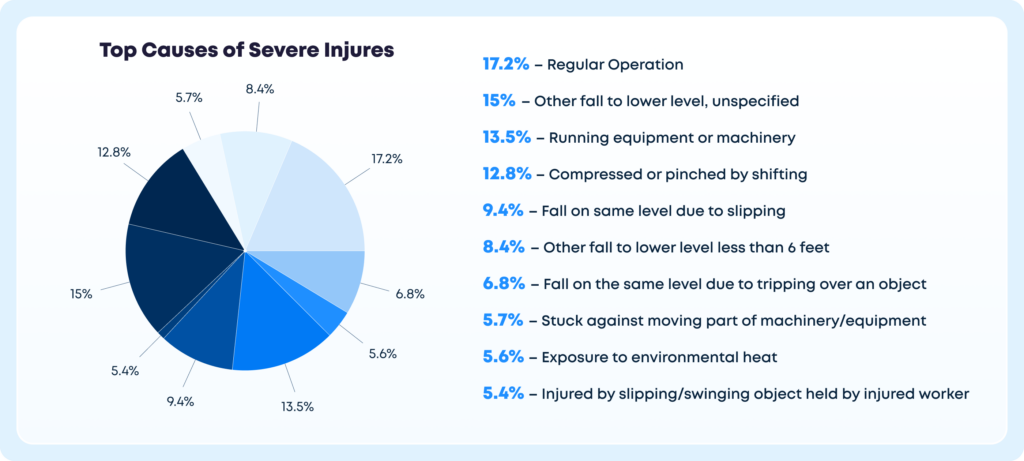
Leading Injury Types
Analysis of the most prevalent injury types revealed a predominance of fractures and amputations among reported severe injuries.
As well as the previous data, these findings highlight the need for comprehensive safety protocols and preventive measures. By addressing the specific risks associated with fractures, amputations, and other top injury types, organizations can tailor their safety initiatives to better protect employees from harm.
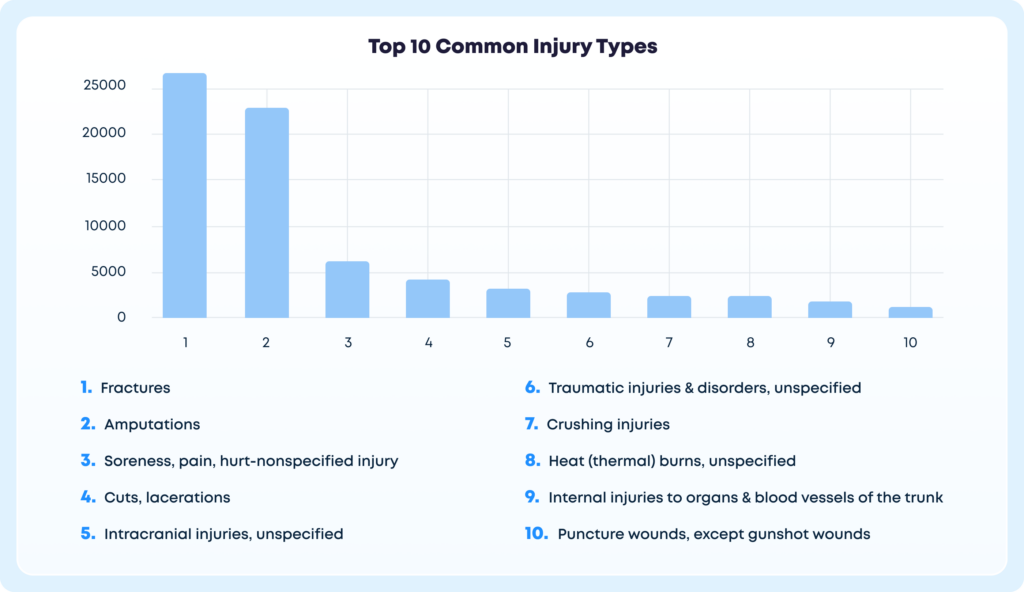
Leading Injured Body Parts
Our examination revealed that fingers and fingertips are the anatomical areas most vulnerable to workplace accidents.
To prevent injuries in these areas, organizations can implement measures such as providing appropriate personal protective equipment (PPE) like gloves, conducting regular equipment maintenance to reduce pinch points, and offering training on safe handling procedures for tools and machinery.
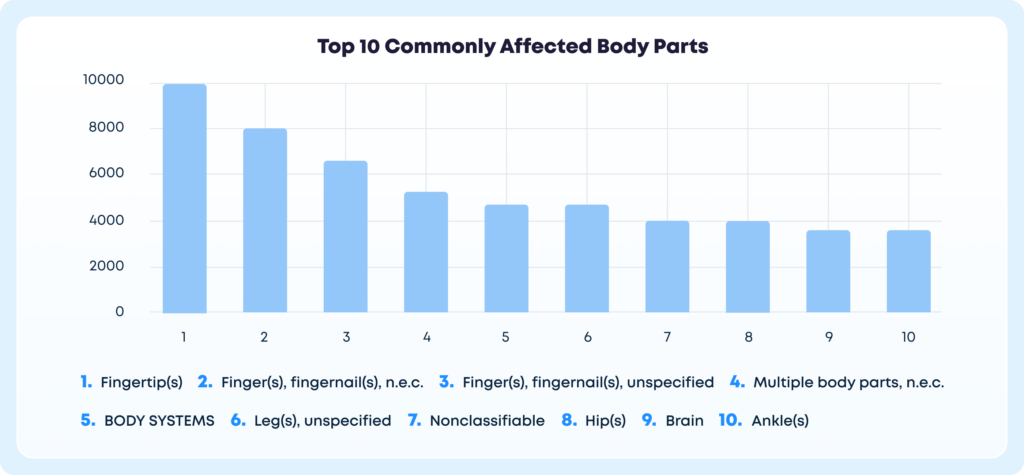
Case Studies for Context
Aside from the raw data, the OSHA’s report contains case studies to illustrate the hazards and risks in various industries, highlighting safety lapses and areas for improvement.
Each incident presents a unique set of circumstances that resulted in severe injuries, ranging from explosions in steel foundries to falls from heights in manufacturing facilities.
As part of our analysis, we have summarized four case studies from different industries, providing our commens on potential preventive actions. These examples can enrich our understanding of industry-specific risks and inform strategies for mitigating workplace hazards.
1. Furnace Explosion in Nebraska Steel Foundry
Accident: In a steel foundry in Nebraska, a routine inspection turned catastrophic when a furnace malfunctioned, leading to a violent explosion. Four employees working on the melt floor encountered a sudden change in furnace sounds, indicating a water leak.
Despite safety protocols, a piece of slag dropped into the molten metal, triggering a rapid expansion event. Two employees suffered severe injuries: one endured burns and abrasions to the face and neck, while another sustained a concussion and contusions.
Injury cause: Malfunctioning equipment, specifically the furnace, led to the accumulation of slag, triggering a violent explosion.
Part of body injuried: Brain
Preventive action: Regular maintenance and inspections of furnaces and other equipment to detect and address potential issues before they escalate. Implementing essential safety documents and protocols for handling furnace operations and emergency procedures in the event of malfunctions.
2. Flash Fire at Oklahoma Oil and Gas Site
Accident: At an oil/gas wellsite in Oklahoma, a flash fire erupted during maintenance operations, injuring three employees. While power washing the heater treater vessel, a sudden ignition caused fire and molten metal to engulf two workers.
One employee suffered fractures and burns to the face and arms, while the other sustained second-degree burns to the hands and first-degree burns to the face.
Injury cause: Ignition of flammable materials during maintenance activities, such as power washing, in the presence of combustible substances.
Part of body injuried: Multiple body parts.
Preventive action: Conducting thorough risk assessments before commencing maintenance tasks to identify potential fire hazards. Implementing proper isolation procedures, including the use of lockout/tagout protocols, to prevent inadvertent activation of equipment during maintenance. Providing employees with appropriate personal protective equipment (PPE), such as flame-resistant clothing and gloves, to minimize the risk of burns.
3. Fall from Hopper Car in Texas Railroad Manufacturing Facility
Accident: In a Texas manufacturing facility, an employee working atop a hopper car fell approximately 16 feet to the ground, fracturing both ankles and a leg.
Despite wearing a harness and lanyard, the employee was not secured to the car, leading to a severe fall. The incident underscores the importance of proper fall protection measures and vigilant safety protocols in industrial settings.
Injury cause: Lack of proper fall protection measures, including failure to secure the employee to the hopper car, resulting in a fall from height.
Part of body injuried: Ankle(s) and leg(s), unspecified.
Preventive action: Ensuring the use of appropriate fall protection equipment, such as harnesses and lanyards, and providing comprehensive training on their correct usage. Implementing strict adherence to safety protocols, including the requirement for employees to be securely tethered when working at heights. Conducting regular safety audits, monitoring safety metrics and inspections to identify and address potential fall hazards.
4. Struck by Falling Object in Pennsylvania Concrete Manufacturing Plant:
Accident: During concrete panel installation in a Pennsylvania manufacturing plant, an employee was struck and injured by a falling concrete panel. The incident occurred due to instability in the panel’s placement, causing it to topple over unexpectedly.
As a result, the employee suffered a broken right tibia and torn knee ligaments, emphasizing the necessity of secure workplace practices and proper handling of heavy materials.
Injury cause: Inadequate stability and securing of concrete panels during installation, leading to their collapse and subsequent injury to an employee.
Part of body injuried: Knee(s) and leg(s).
Preventive action: Implementing proper procedures for the safe handling and installation of heavy objects, including concrete panels. Providing training to employees on safe lifting techniques and the importance of maintaining stability during installation tasks. Utilizing appropriate lifting equipment and securing mechanisms to prevent objects from falling or collapsing unexpectedly.
These are only several cases, but implementing preventive actions to address them, can significantly reduce the risk of severe injuries in the workplace, fostering a safety culture and healthier environment for all employees.
Note: It’s essential to acknowledge the limitations of our analysis. The dataset’s scope is limited to severe injuries reported under federal OSHA jurisdiction, potentially overlooking incidents under state jurisdiction. Additionally, the accuracy of injury reporting and classification may vary, influencing the reliability of our findings.
You can find the full OSHA’s report at their website, and analyze more data that can be applicable to your industry.
Unpacking Workplace Safety Insights
Our analysis reveals important implications for preventive measures, highlighting the necessity for adaptive protocols to address evolving risks. We see that tailored safety strategies are paramount for specific sectors, such as enhancing fall protection in construction or implementing machine guarding in manufacturing.
In this context, Fluix can serve as a comprehensive solution for mitigating severe injuries in the workplace.
By digitizing safety documentation processes, Fluix ensures compliance with regulatory requirements, allowing for efficient data collection and analysis. Through its user-friendly app, it facilitates the distribution of safety guidelines to frontline workers, enabling real-time communication and feedback.
Moreover, Fluix’s customizable workflows empower you to implement preventive measures proactively, track inspections, analyze findings, and identify areas for improvement. By using smart automations, businesses can minimize the risk of severe injuries and promote a safer work environment for all employees.