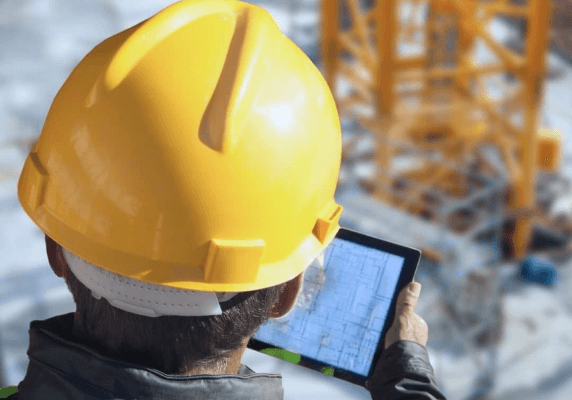
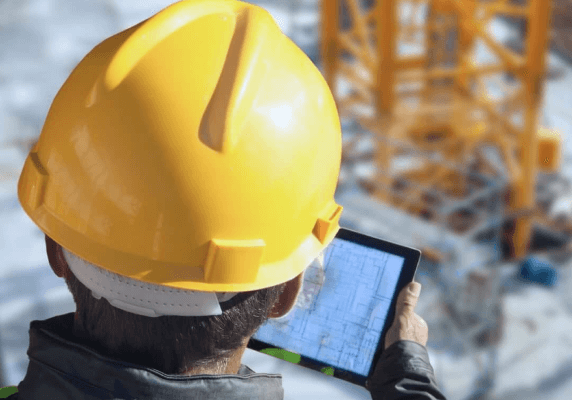
Construction
Site inspections, field level hazard assessment, safety walkthroughs, commercial building inspections
See more use casesAutomate and standardize your inspection processes,
making a meaningful impact on safety & compliance with Fluix
Capture any inconsistency to ensure
on-site safety and avoid legal issues
Analyze incidents and near misses, mitigating risks and reducing incident rates
Share reports with stakeholders, ensuring everyone is informed about the findings
Capture exact site conditions and report issues from your mobile or tablet with the Fluix field inspection app
Avoid Safety Issues Due to Under-Reporting Learn MoreAutomate each stage of inspections, assign tasks to team members’ to-do lists and save time on every inspection
Standardize Inspections Across All Teams and Locations Learn MoreOur team is here to guide you through everything you need to know:
creation, customization, security, and ROI potential
Get your field crews updated on process changes, and keep up with multiple sites without having to visit them
Improve Operational Efficiency with Effective Communication Learn MoreGet Fluix reports as detailed as you want them to be, with numerous customization and sharing options
Create Detailed Reports That Reflect All Activities Learn MoreAzure
Dropbox
Zapier
Procore
Salesforce
Microsoft 365
Pipedrive
Monday
Power BI
Integrate Fluix with your preferred data analysis systems such as PowerBI,
Tableau and more.
Establish connections between Fluix workflows and your team’s tools via Zapier,
eliminating friction between teams, locations and projects.
If it’s listed below, then YES!
Site inspections, field level hazard assessment, safety walkthroughs, commercial building inspections
See more use casesRegulatory compliance, flight operations inspections, integrations with MRO systems
See more use casesTurbine inspections, QA reports, offline mode, asset management, integrations with SCADA systems
See more use casesField inspections, maintenance inspections reports, HVAC work orders
See more use casesHave question about how to do it? Our team is here to help