What Plant Inspection Software Does
The core function of the plant inspection software is to set up and automate the process of inspection, eliminating manual work and human errors as a sequence.
The first step to configure such a process is to identify roles and responsibilities. The key players in performing plant inspections are usually Site Managers and Technicians.
The Technician performs the inspection and completes the plant inspection checklist. The Site Manager reviews the checklist . The reviewing process is much more than a quick glance at the names, dates, and checklist items. It’s a strong ‘Yes’ to final submission, which in turn, gives a go-ahead for a plant to be in use.
Here below we’ll look at how Fluix Taskstream allows to manage such a process.
Example of a Plant Inspection Workflow
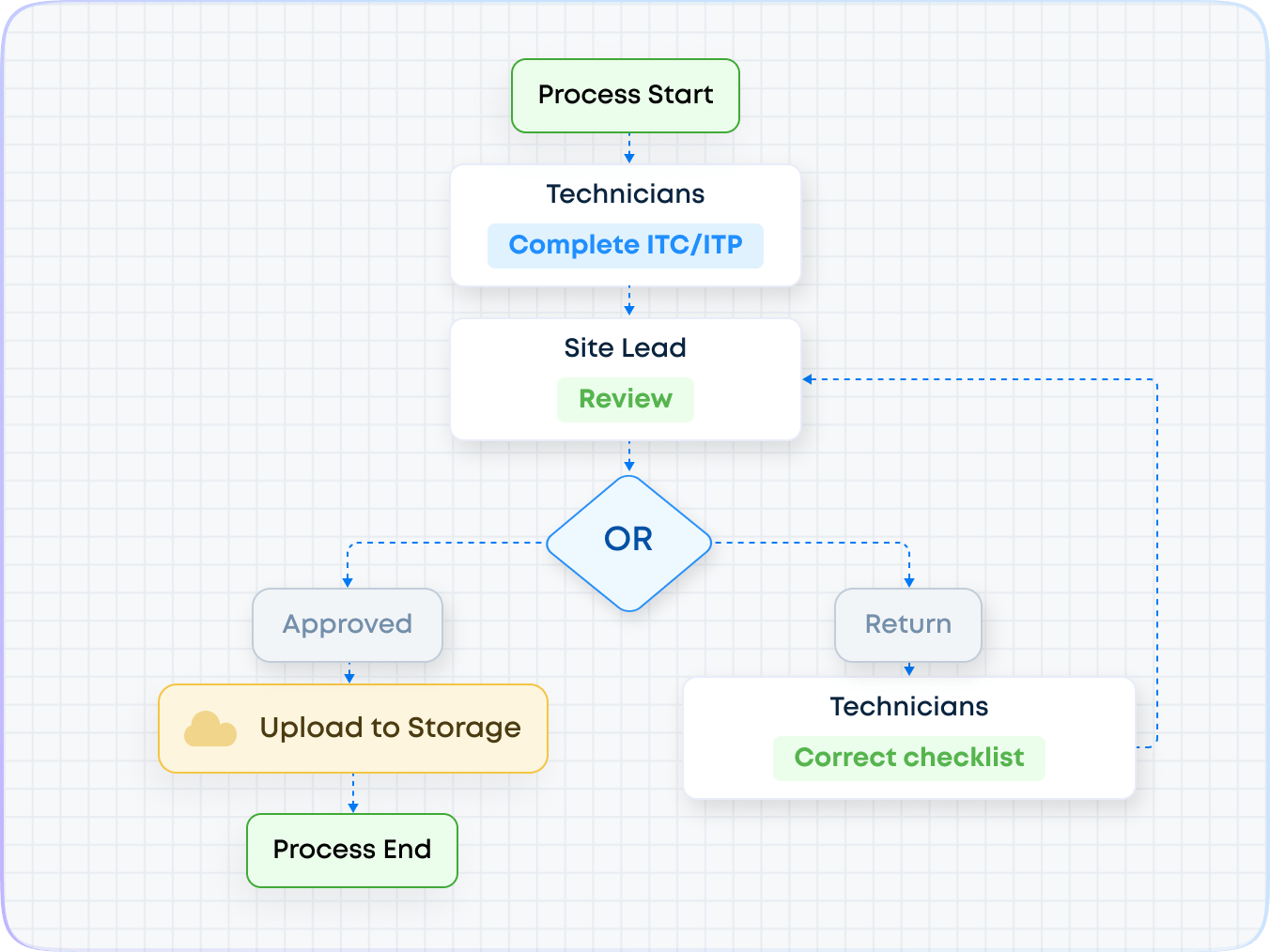
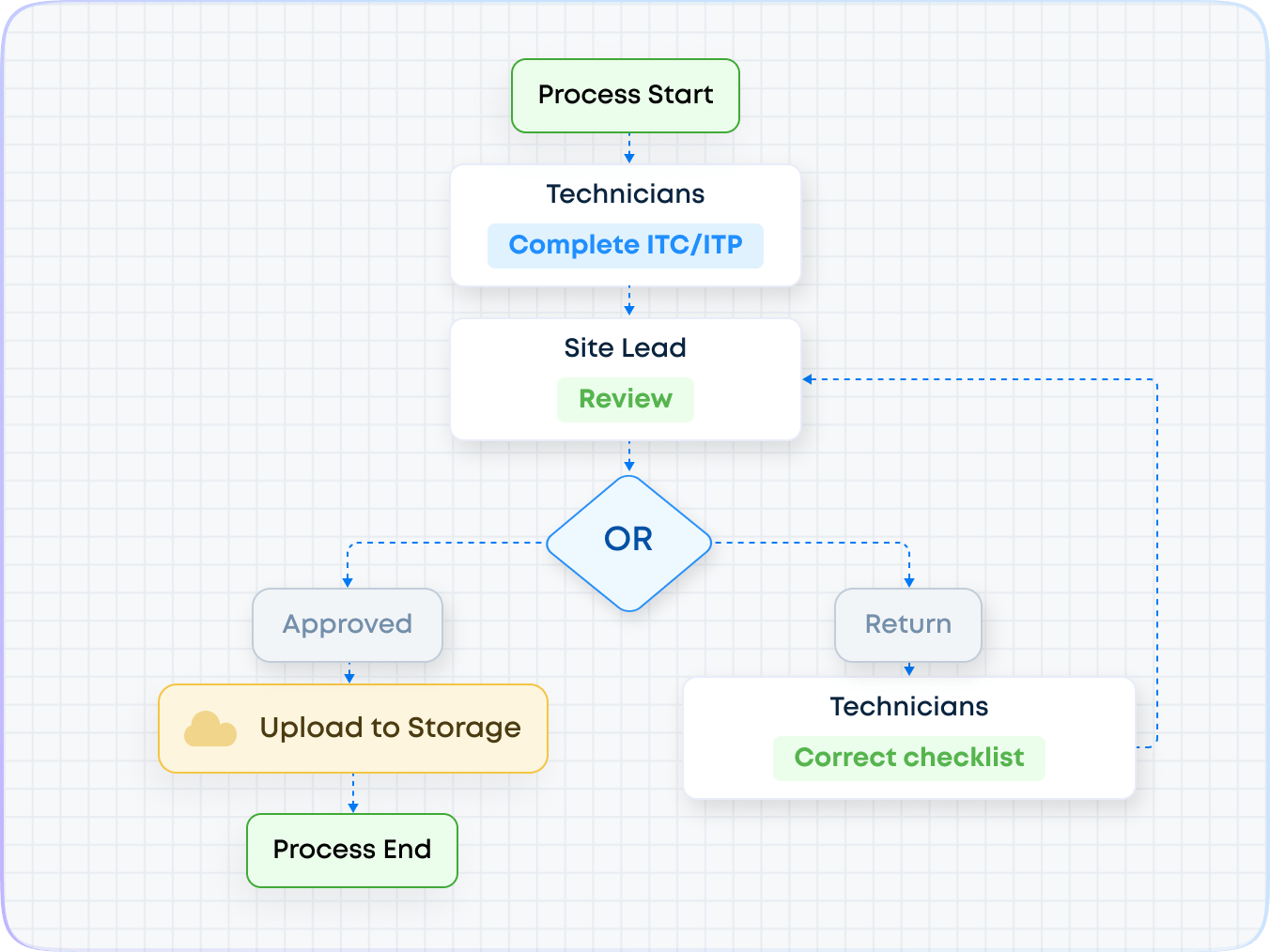
Here are the steps:
- The technician opens the inspection test plan template in the mobile app and completes it as part of the – inspection process.
- Once the ITC/ITP is ready – the technician submits it down the workflow.
- The Site Manager receives the ITC and reviews it. If the document is completed without errors, it is submitted to the cloud storage. If the ITC requires some corrections, it is returned to the Technician for editing and for another round of review and approval.
To build this workflow in Fluix, all you have to do is drag and drop chart elements, adding actions names and performers.
To cover the key aspects of the process, we recommend using these checklists:
Benefits of Using Plant Inspection Software
A proper software should help maximize the efficiency of plant inspection and management. The efficiency includes several aspects below.
- Fast document delivery
Plant inspection reports, time sheets, delivery notes, work reports, shipping documents, checklists and other documentation are digitized, up-to-date and available for the remote teams at any time. - Process transparency
An automated workflow aims to overcome misunderstanding between the teams. Everyone knows when to start and finish their part of the job, and who is the next in the process to collect data, review, or approval. - Compliance
Fluix cloud storage helps – keep all daily plant inspection checklists and reports in one place and get all the data available for audits. - Speedier data processing
Using mobile forms, the technicians can submit their checklists and plant inspection reports right аrom smartphones or tablets. The office receives aggregated data from the technicians in a structured report. That information helps identify the emerging trends and modify future inspections.