Preventing possible risks before they could happen is what good companies first and foremost care about. To err on the side of caution, field workers run inspections to see whether the equipment is suitable for further operation and use. As the number of items to be checked on the field is heavily high, there should be a method making time spent heavily low — which is workflow automation. This is the moment when an equipment inspection software gets into a game.
Refocusing on Equipment Inspection Software
Field workers face different challenges everyday: strong wind, pouring rain, burning sun or just a human factor as being in no mood. In such cases inspection paperwork becomes even more annoying, and to ease the job, you can replace paper forms with a tablet or smartphone with the right equipment inspection app installed on it.
Let’s take a look at how the equipment inspection software helps field teams perform inspections, fill in equipment inspection checklists, get approvals, and send reports being anywhere, even on the highest point of the turbine or building.
All that is done via an automated workflow – repetitive series of tasks configured for each team in an order that allows to cover all business needs, from simple data collection to reporting and analysis.
Example of an Equipment Inspection Workflow
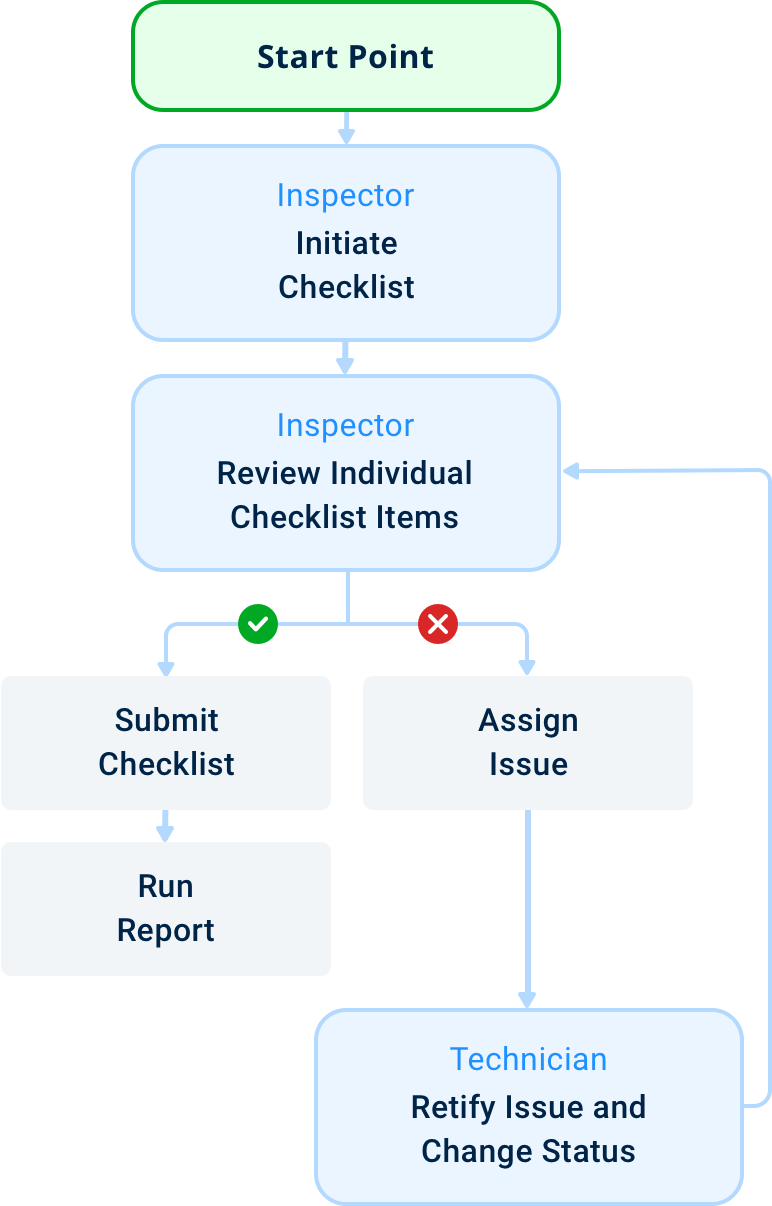
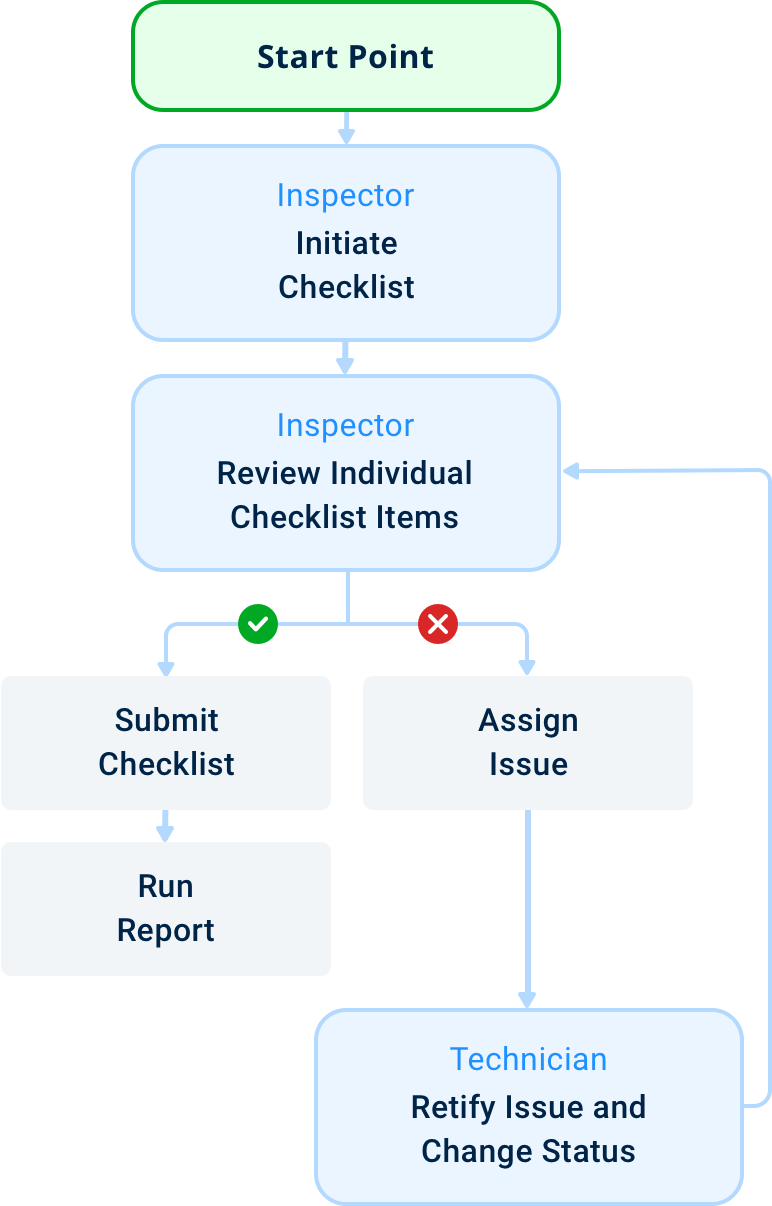
The steps are:
- The Inspector takes the equipment inspection checklist and fills it out, going through the items. If everything is in order with the equipment, the report is filed. If there is an issue with the equipment, the Inspector assigns the checklist to the Technician for inspection.
- The Technician takes the equipment inspection checklist under review to get to know about the problem with the equipment. When the issue is fixed, the technician submits the report.
- The data from all completed checklists is extracted into a dataset and analyzed to make data-driven decisions.
It’s easy to create similar workflows in Fluix — equipment management software that helps companies automate processes of any complexity. So, let’s make a stop to spread a bit more light on things that make automation a useful process for your business.
To cover the key aspects of the process, we recommend using these checklists:
Going mobile with digital
- There is a better alternative to paper binders. Instead of printing everything from one of the offices and then sending it by mail to people in the field, you can put that information in cloud storage.
- With digital checklists your field team will gain accuracy, avoid human error that was present when their binders were filled out by hand with sloppy handwriting.
- Ability to take photos and add them to the form in one click saves time both for the field team and then the office manager who reviews the checklist and processes information.
- Barcodes scanning on equipment is a valuable tool to save time on both entering information manually, and accessing needed files right in the app.
Efficient Review and Approval Process
Fluix allows you to build as simple as complex approval processes as it’s needed, including multi level approvals. An engineer, having received an equipment inspection form with comments and annotations previously added by a technician, can easily navigate to these annotations for review and resolution. So, every team member is involved and no detail is overlooked.
Using Data to Foresee Downfalls
The standardized forms ensure the data that is initially captured in equipment inspection checklists, is well structured, reliant, and ready for reporting. Fluix allows you to automatically retrieve this data from the completed checklists and aggregate it in “datasets” that you can export at any point of time to Excel or any data intelligence tool of your choice. In this way, you get a snapshot of most frequent issues, defects, and can prevent equipment downtime.