Production shutdowns and labor shortages have posed significant challenges to manufacturers in recent years. These market realities are driving technological innovation as firms continue to adapt to ongoing supply chain and workforce issues. Find out how process industry automation can change the way manufacturing works.
Process Industry Automation
Process automation is becoming a standard practice for manufacturers around the world. This measure can involve using software to automate any aspect of operations or a combination of workflow and production management software with specialized robotic equipment.
Automation has the potential to optimize every aspect of operations. Office staff can be freed up from redundant tasks to focus on skilled and value-added workflows. Workers on the factory floor may also see their job descriptions change, as automation is particularly useful for managing and minimizing safety risks.
How To Define Automation in Production
Manufacturers can try to automate aspects of daily operations, procurement, assembly, manufacture, quality control or distribution. Many firms start with office-based workflows and extend these improvements to more aspects of a master production schedule. Here are a few general definitions of areas of production in which automation is possible:
- Operations and workflows: The daily workflows of a manufacturing firm can be relatively easy to automate. In this area, automation allows for processing order forms and employee requests with minimal manual input.
- Procurement and tooling: Ordering supplies to make products and tooling components can also be automated. Look for software that analyzes employee input or sensor readings to monitor stock levels and equipment conditions.
- Quality assurance and control: Automated quality control can back up employee inspections. Product quality data can also be used to refine manual or automated production processes.
- Assembly and manufacture: Smart production management software and robotic tools appeal to many manufacturers. This approach to automation may involve customized systems and specialized tools.
- Order fulfillment and shipping: Non-production aspects of manufacturing can be automated with the same system used for daily operations or by integrating dedicated platforms with workflow software.
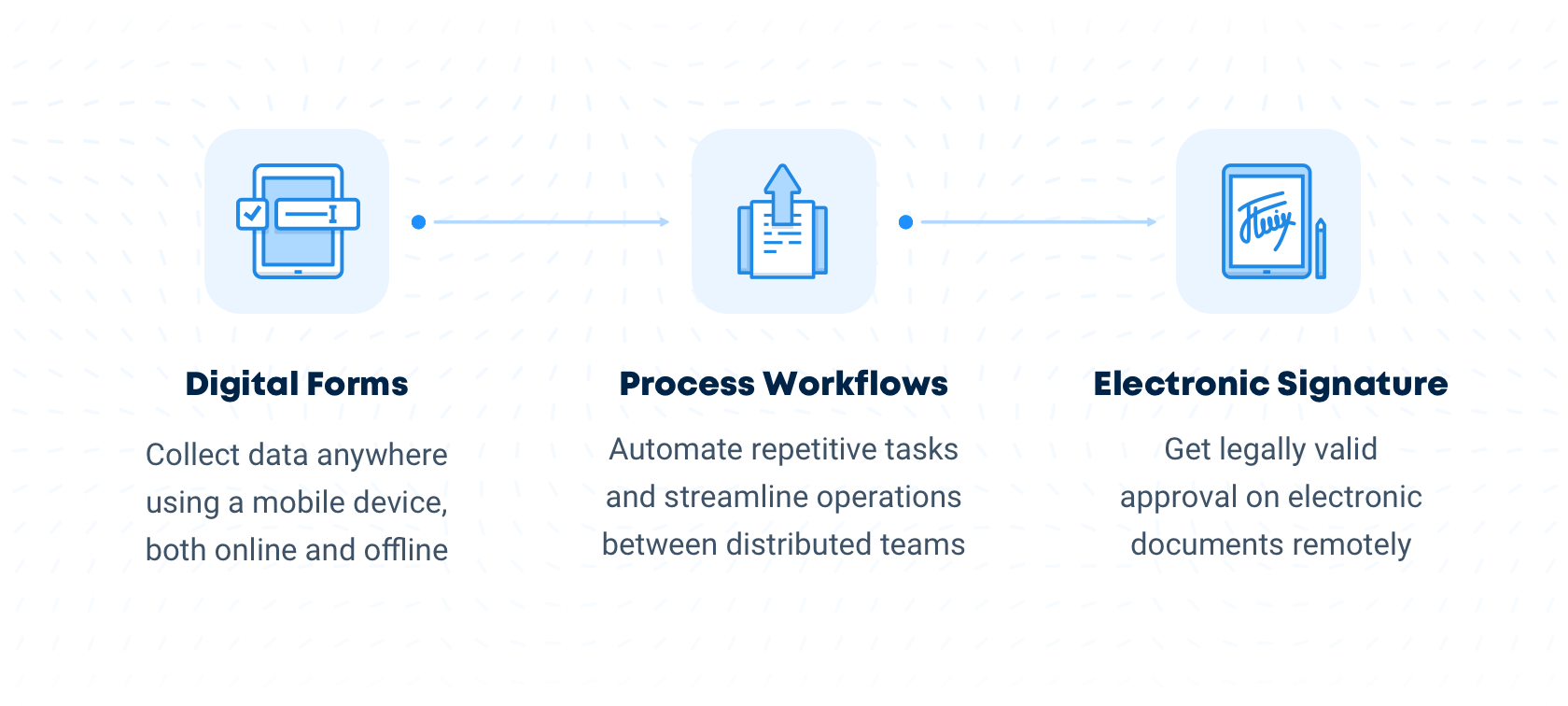
In every sense, automation involves reassigning the work of monitoring and controlling the production and delivery of products and services from humans to machines. A human workforce is still integral to most manufacturing operations, and these jobs can be improved by combining automation with oversight from trained workers.
Industrial Machinery Trends
Trends in industrial machinery point toward smart systems that can be paired with production management software to automate more aspects of operations. Manufacturers that are committed to automating a variety of aspects of production may be interested in investing in next-generation software and hardware for smart factories.
In addition to automation capabilities, the most innovative production management platforms have tools for monitoring the operating condition and maintenance needs of machinery. For maximum productivity, manufacturers can integrate systems to allow stakeholders to monitor operations and manually exert control as needed.
Read Next:
Post-COVID Trends in Aviation
As Covid-19 formed its grip on the world, airlines are looking for operational efficiency gains more than ever before


Robotic Process Automation
Many aspects of manufacturing already involve systems. Most software can be controlled on the user interface level by bots developed for the purpose of robotic process automation. Tasks that involve repetitive input or data transfers can typically be set up to occur automatically. The effects of RPA can be felt across every workflow pertaining to production.
Prior to production, it may be possible to automate stock monitoring and ordering. These systems can also make it possible for manufacturers to track and find ways to cut costs while preserving the quality of finished products. RPA can be useful for managing many systems that run behind the scenes at manufacturing firms.
Manufacturing Market Trends
Beyond automation, a number of innovations are poised to transform the face of manufacturing during the next decade. Most of these technologies are related to automation or can be automated during implementation. Here are five industry-wide trends that manufacturers on the cutting edge should consider:
- Additive manufacturing: 3D printing or additive manufacturing is becoming more commonplace. More options for systems and materials are available, and equipment costs are going down.
- Augmented reality: Augmented reality glasses and headsets can be used to train workers on how to use equipment in real time. Some of the most promising applications for AR are in manufacturing.
- Digital twin technology: Interactive modeling technology that draws on real-time data is useful for predictive analysis. Many major companies use digital twins.
- Machine learning: Machine learning goes beyond artificial intelligence to enable machines to learn from data without programming. There are significant applications for ML in manufacturing.
- Process automation: Setting up manufacturing processes to occur without manual input is a goal for many firms. A combination of software and hardware, such as robotics, may be necessary to pursue process automation.
All of these trends fall under smart factory initiatives for long-term market viability. Based on the type of products manufactured, any of these trends could be worthwhile to pursue.
Growth in the Manufacturing Sector
A global manufacturing growth rate of 7% and a machinery growth of 6.5% are projected for 2022. Supply chain instability and workforce shortages are the most likely limitations marketwide and for individual manufacturers.
Pursuing automation and other smart factory trends can help a firm meet annual productivity goals. This year is also a good time to invest in automating workflows and production processes and pursuing other innovations that should pay returns for years to come.
How Manufacturers Can Stay Current
Staying up to date on industry news can introduce stakeholders to the latest innovations that could facilitate production and increase profits. Industry publications often showcase new technologies in manufacturing that could transform production processes.
Taking the time to develop an accurate master production schedule also lays the necessary groundwork for automation and the implementation of other technology. Production data can also be analyzed and optimized to minimize waste and maximize productivity.
Process industry automation saves many enterprises time and money in the long run. Automation involves an up-front investment but can ultimately raise the bottom line of a manufacturing firm. Conceptualizing, digitizing and automating workflows are all helpful ways for firms to prepare to upgrade manufacturing processes.